Airformed Culverts
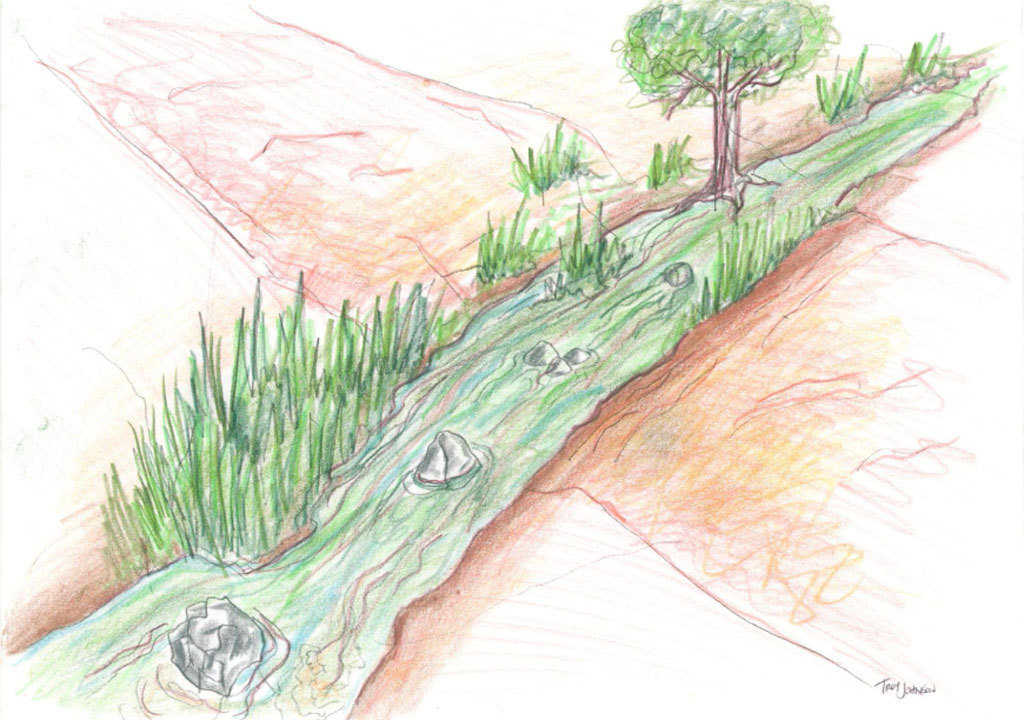
Example — This is an example of a river crossing a road, that would prevent people from crossing in some circumstances.
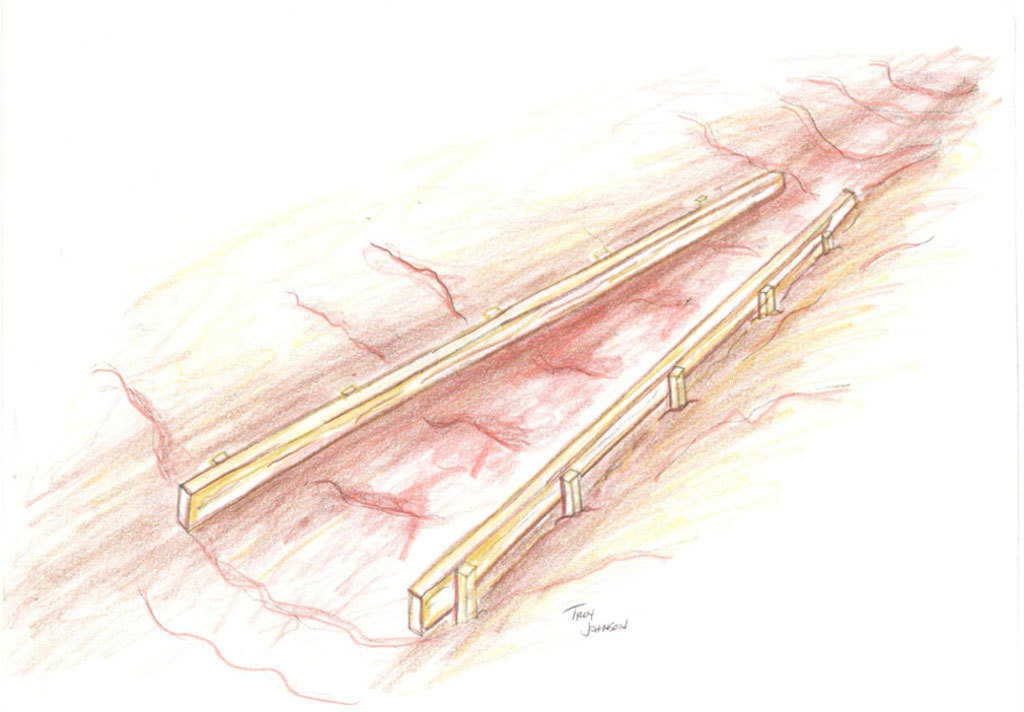
Forms for bottom — The water first diverted temporarily, while crews will form the bottom part of the culvert.
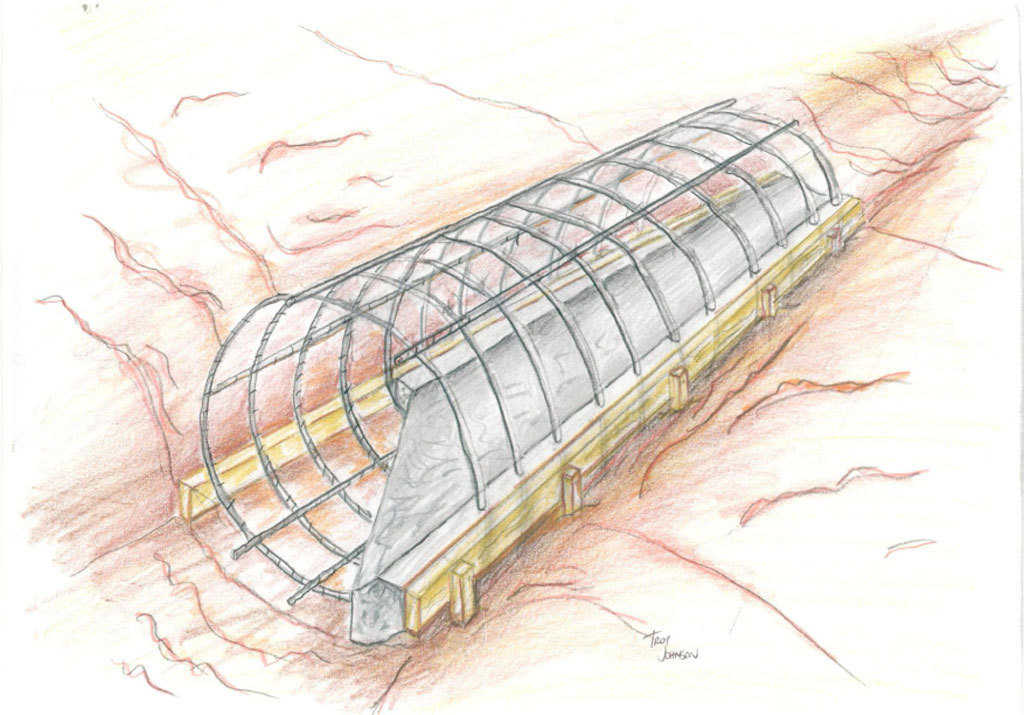
Set rebar — Now the crews will make the rebar cage needed to reinforce the concrete and place it in the hole. Then concrete is poured to form the bottom of the culver, and to hold the steel in place.
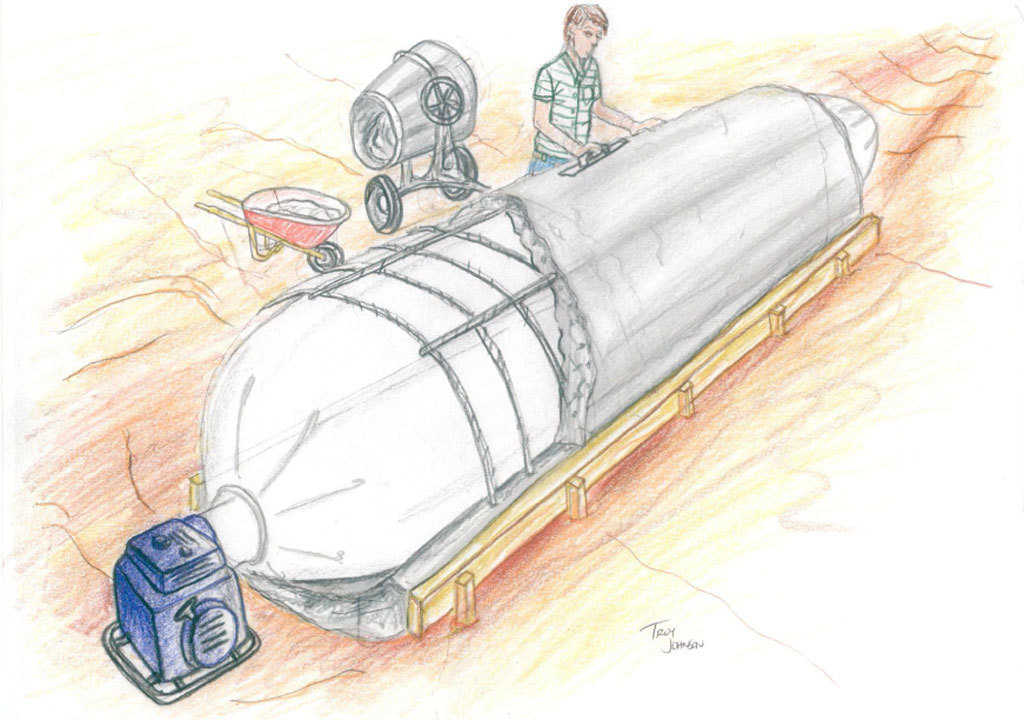
Airform inserted — Now the Airform is slid into the rebar cage and inflated, making an easy job out of applying the concrete by hand.
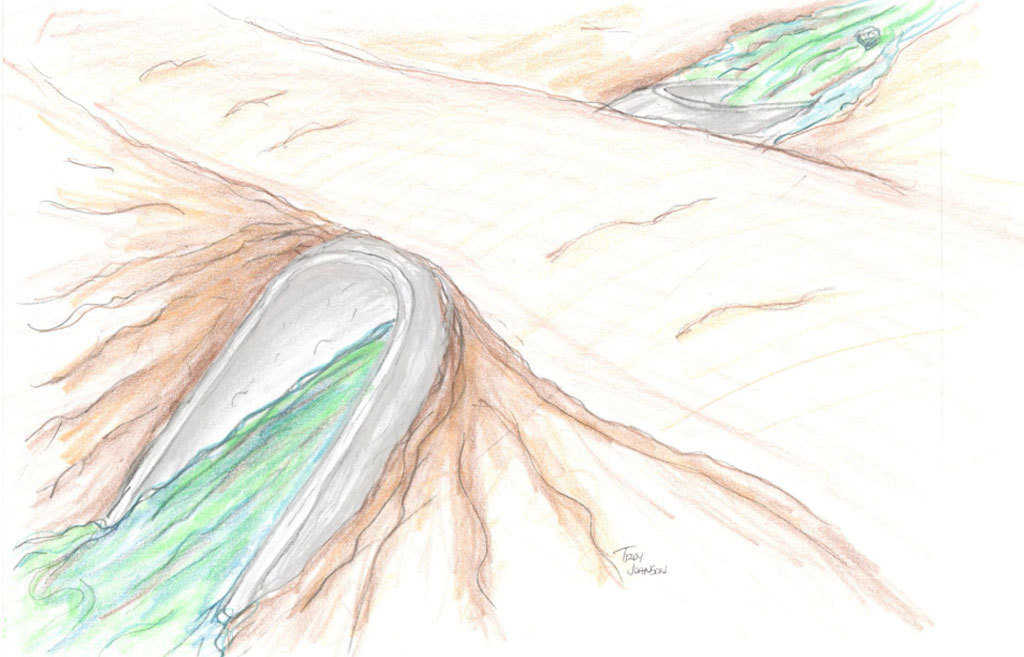
Finished culvert — Once the concrete dries, simply slide the airform out to be used again and again. The dirt can be backfilled in a few days, and you have a simple, permanent, culvert.
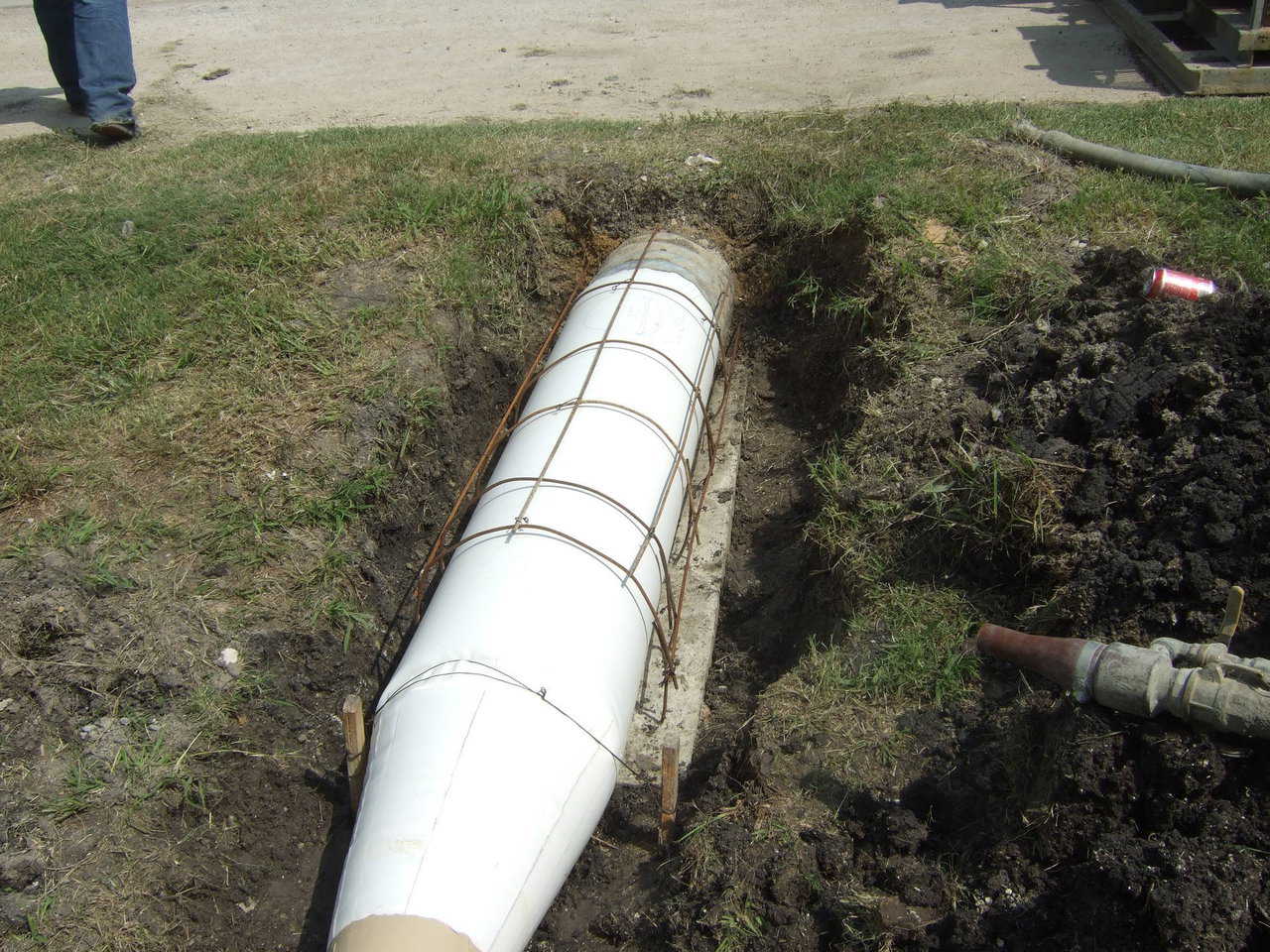
End Cap — We used this technology to spray some end caps on the ends of our existing culverts. These culverts had been damaged by trucks, so we bent them back to shape and used out Airform to spray on new ones.
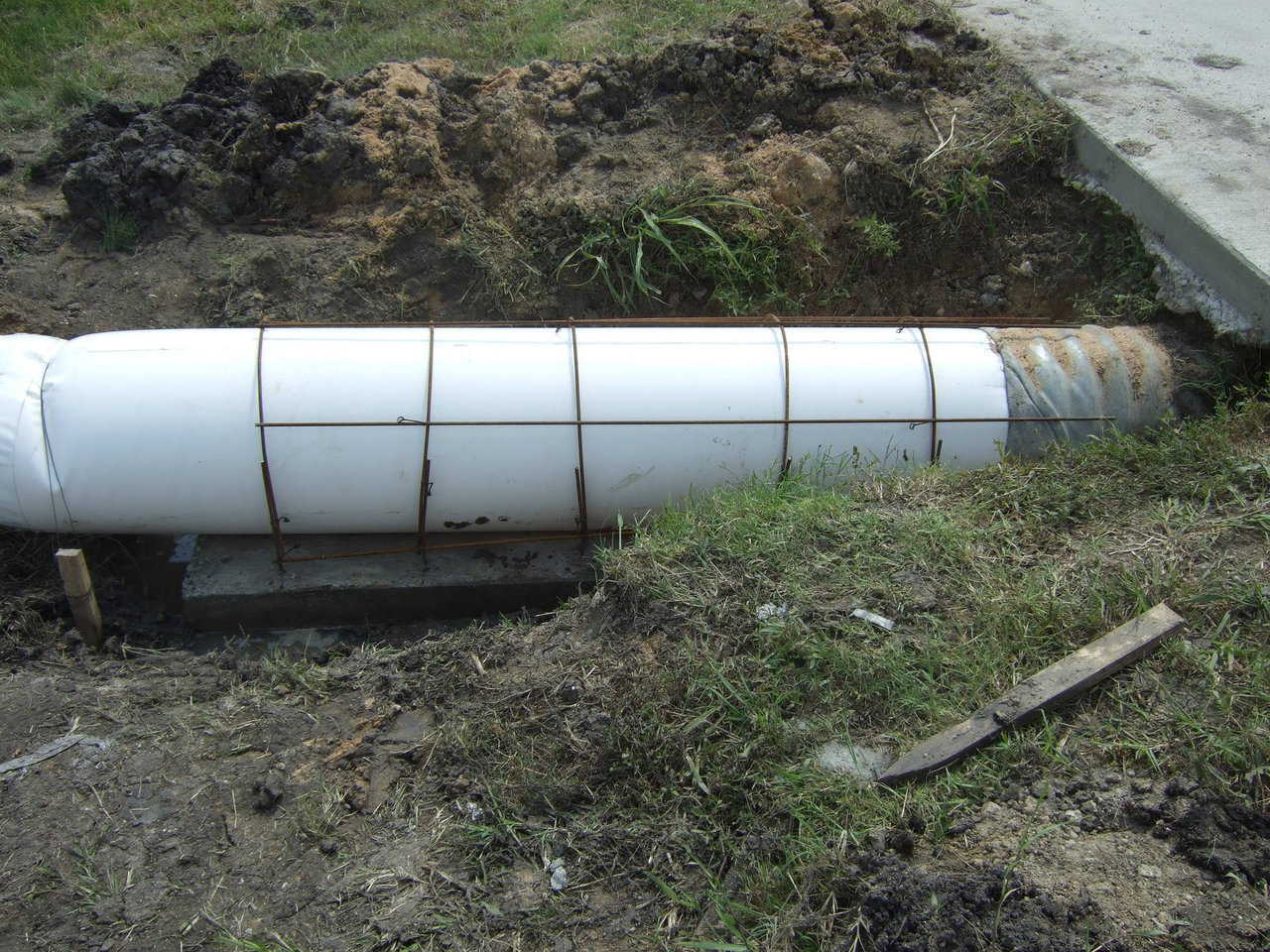
Ready for concrete — Here the bottom has already been poured with the steel embedded. Now the crews have inflated the form, and will begin to spray shotcrete on the outside. This could just as easily be done by hand, and in many places is more efficient.
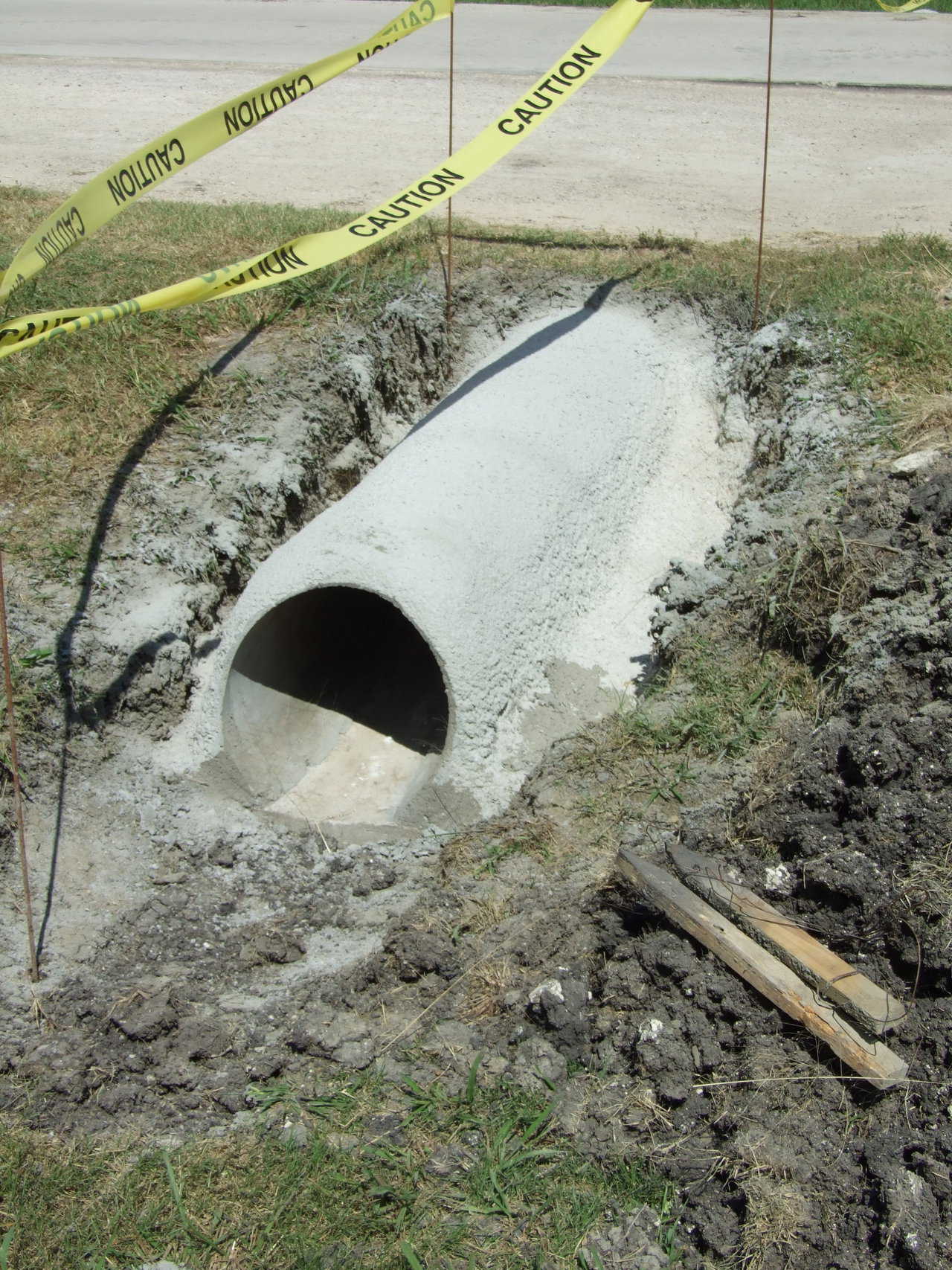
Finished culvert — This is a finished culvert that was sprayed in Italy, Texas.
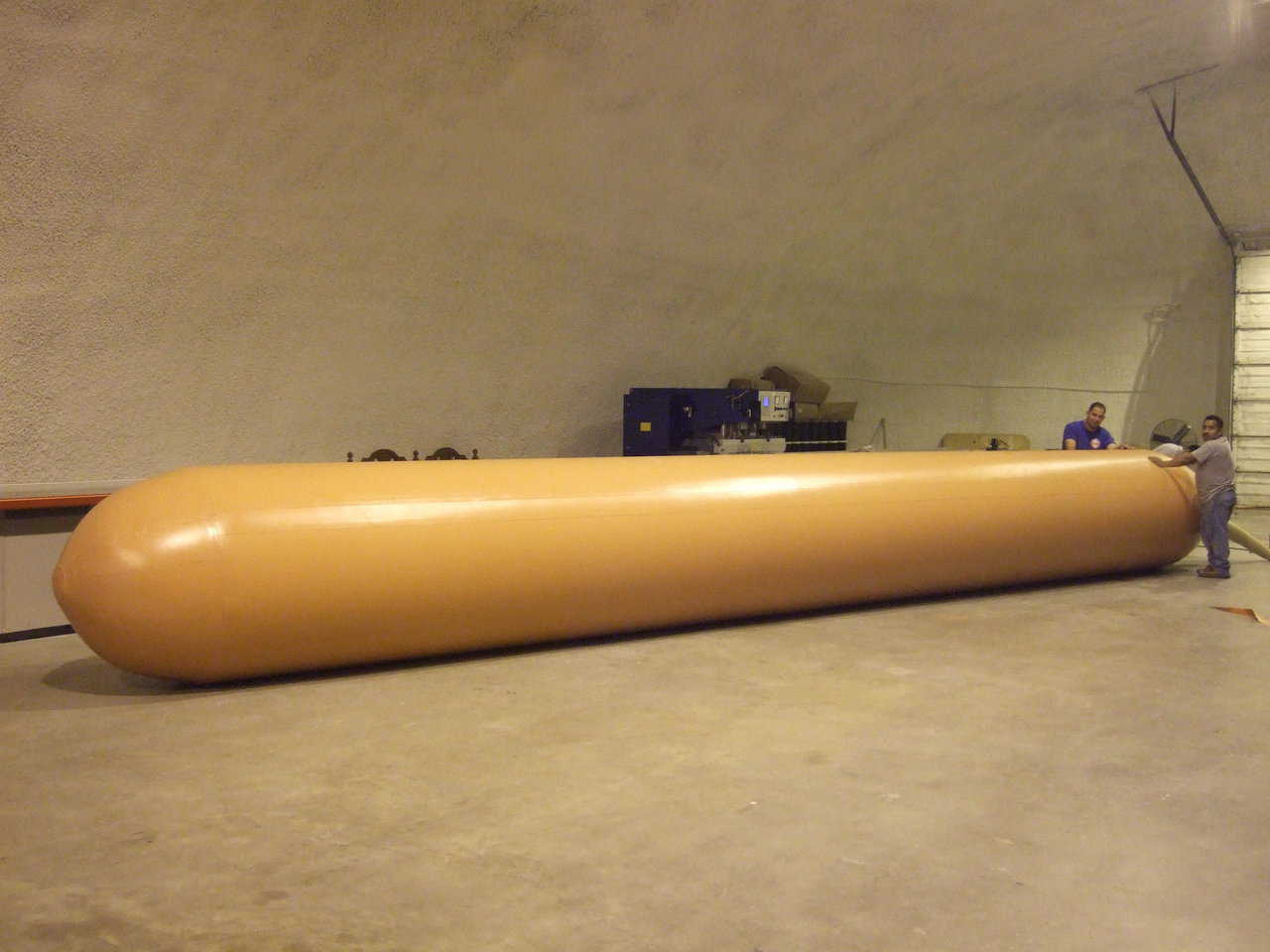
Airform being tested — This is a 10 meter long culvert Airform that is being tested at our facility in Italy, Texas.
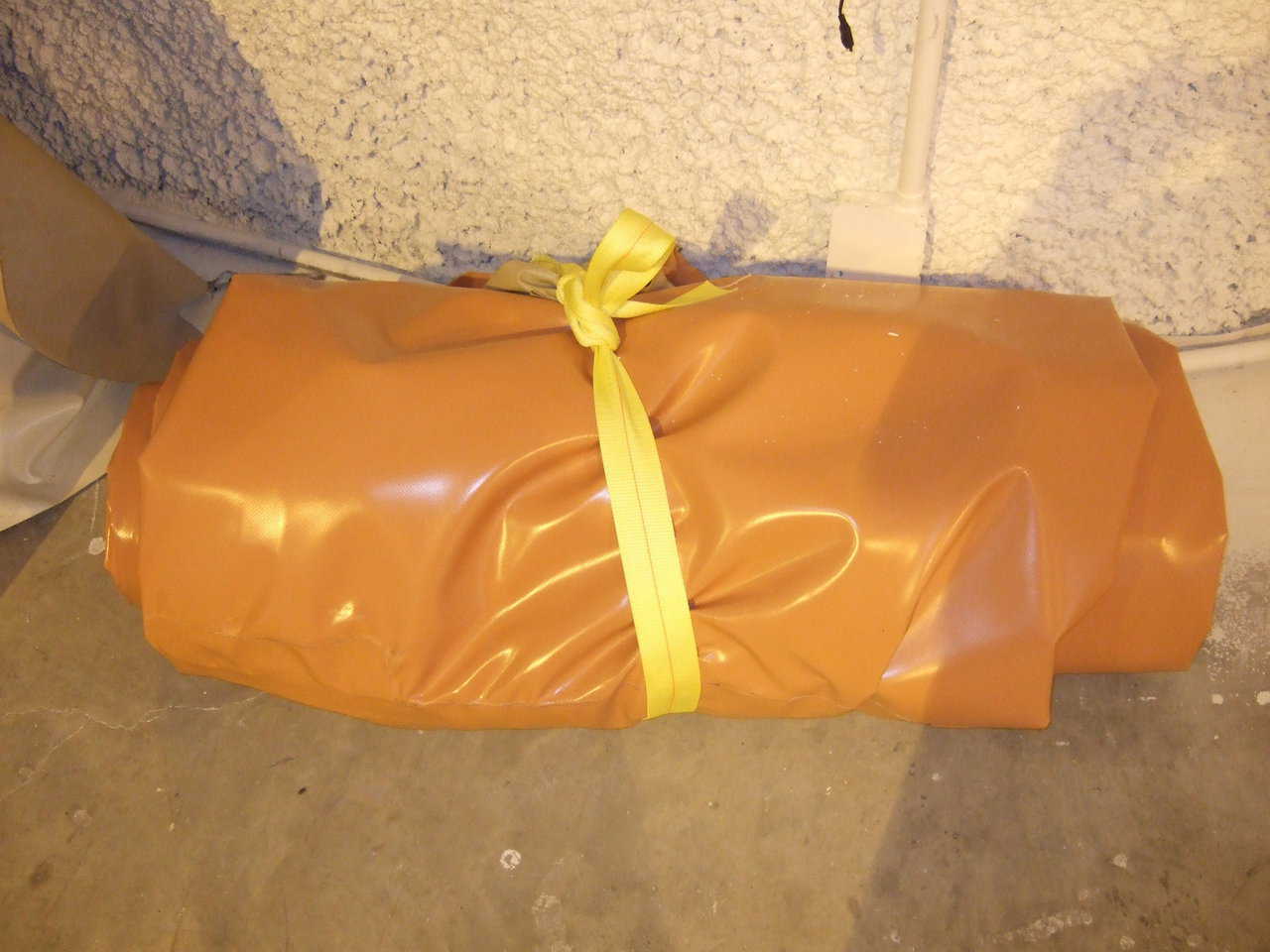
Easy to transport — This 10 meter long culvert Airform can be easily transported by one man to any destination, making it extremely versatile.
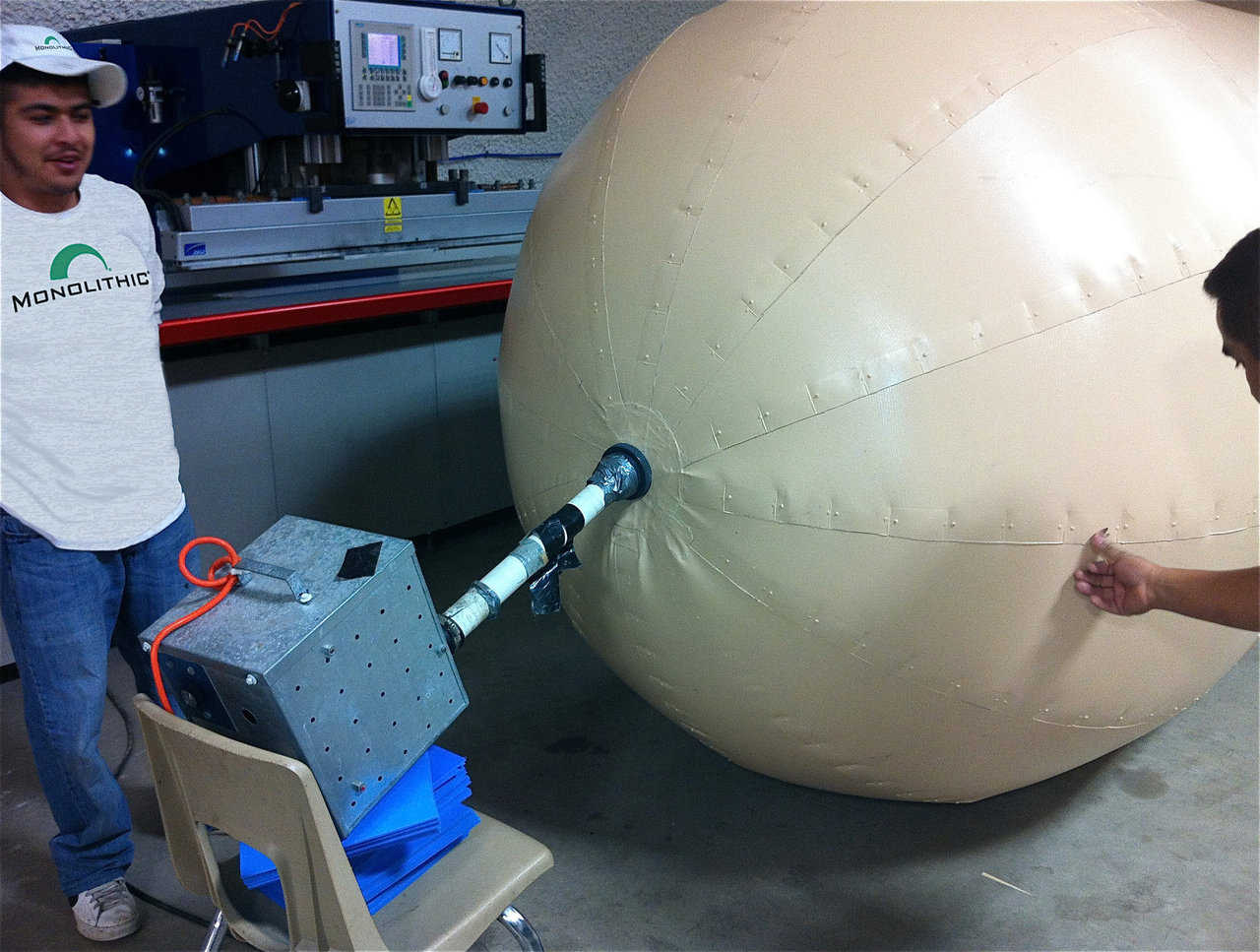
This small inflator fan is all that is needed to keep the airform inflated.
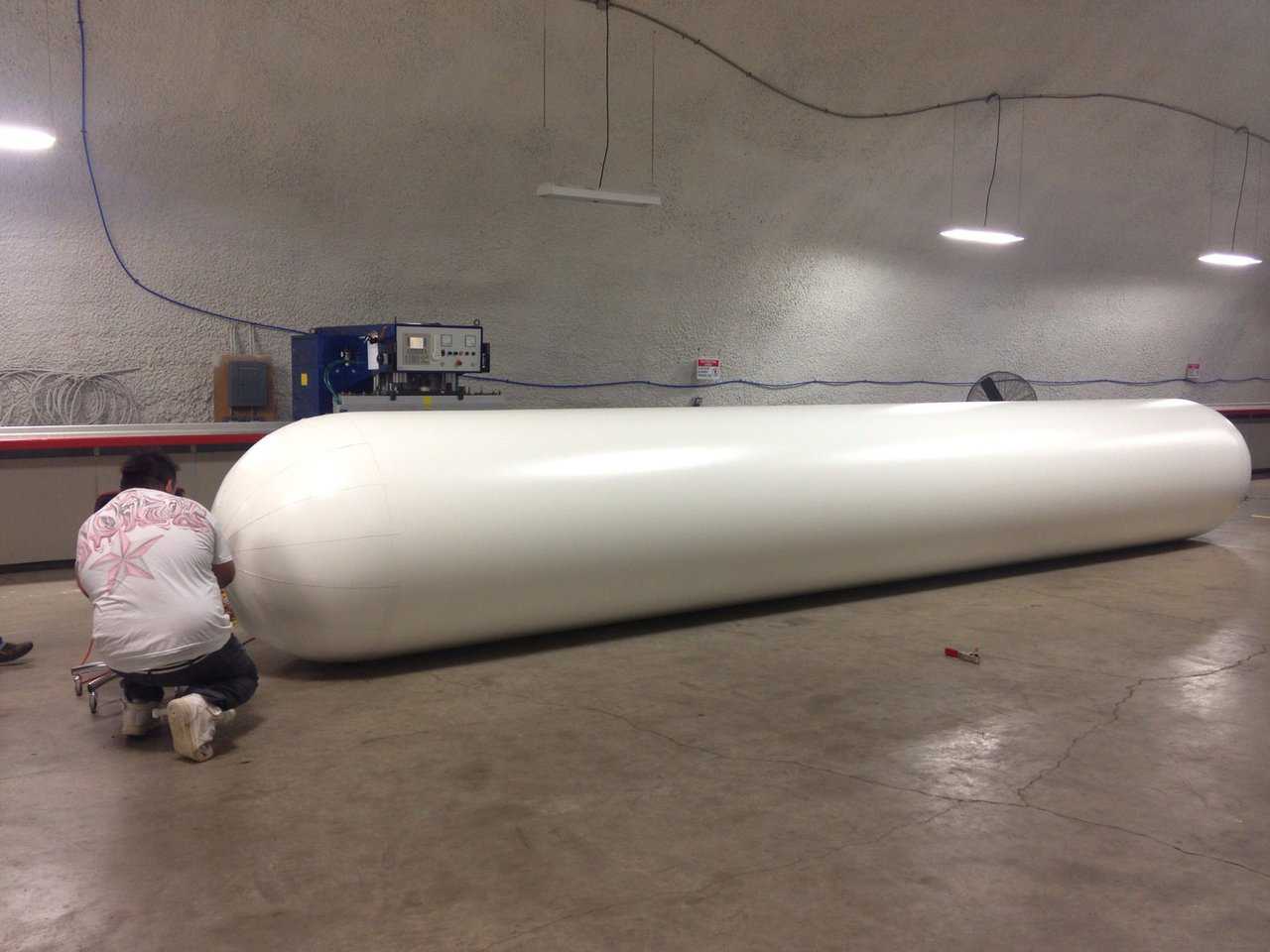
These culvert forms can be any size. The one shown has a diameter of 125 cm (7 ft) and a length of 8 meters (26 ft). Monolithic culvert forms are designed and built to last for centuries. They can be reinforced with basalt rebar that will never rust. (Don Garrison)