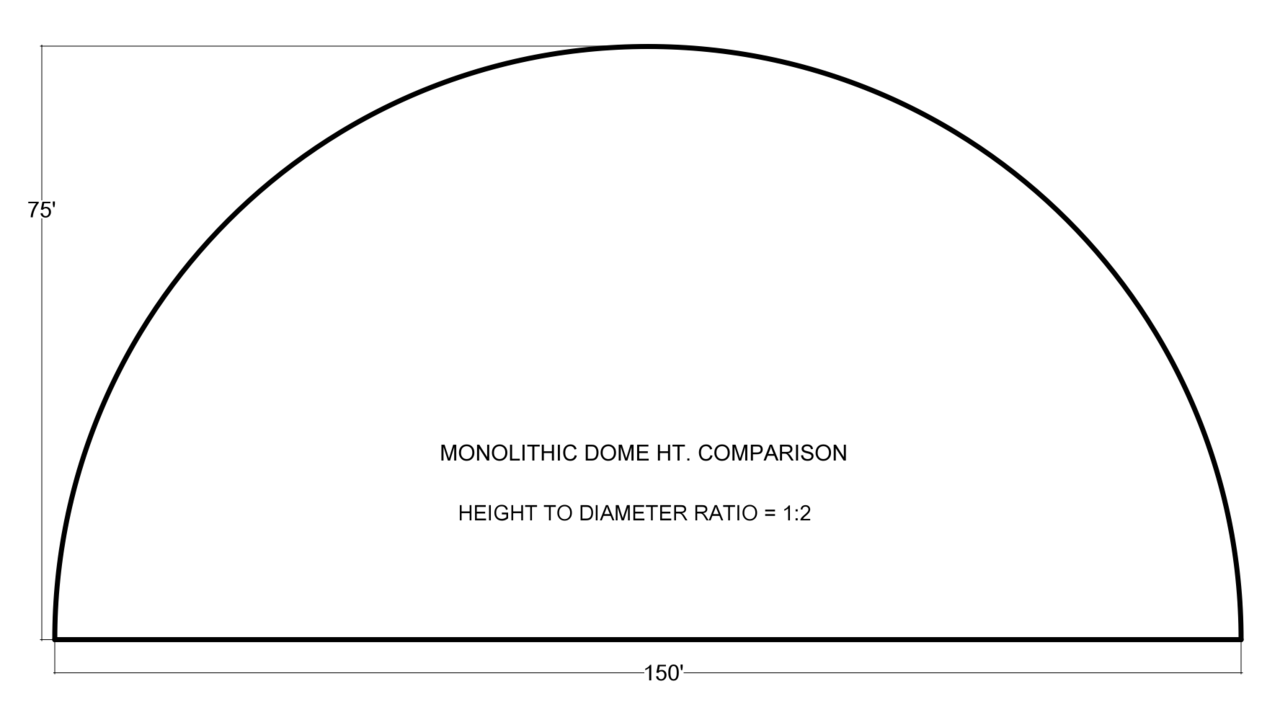
DOME PROFILE 1:2 – The half sphere shown here is 150’ wide and 75’ high. This profile is ideal for bulk storages with the capacity to hold tremendous loads of fertilizer, cement, etc. The height helps hold the loads and makes putting product in and out of the dome relatively easy. Half spheres can be built on vertical walls, but you get the most for the least with the spherical shape without the cylindrical stemwall.
The Dangers of Low-Profile Monolithic Domes
When I started the Monolithic Dome business, I partnered with Dr. Arnold Wilson, who had been teaching thin-shell engineering for twenty years at Brigham Young University in Provo, Utah, and had engineered quite a few domes. I knew instantly that he knew far more than I did about thin-shell dome construction. Dr. Wilson not only followed in the footsteps of the thin-shell dome pioneers, he expanded on their concepts.
Dr. Wilson was a thin-shell dome expert who knew by calculation and experience, the complicated nuances of building domes.
He had built enough domes that he knew there had to be a strict margin of safety in place with both the engineering calculations and with the building methods. He knew the importance of weighing the theoretical against reality and experience, and that there are many, many cases where the reality is imperative.
One of the reality points is the Monolithic Dome’s profile. Caution must be exercised with the dome’s profile, especially with Monolithic Domes because they are built using an Airform membrane. Inflated forms, by nature, are not absolutely precise. When you inflate a membrane, its shape cannot be perfect.
Theoretical calculations are always based on the assumption that every factor is perfect, when in reality, this is never the case. Tiny mistakes and imperfections can add up to catastrophe.
Error can be introduced in the patterning process by the person doing the math. Little mistakes are extremely difficult to see. Error can also be introduced by the fabric used to make the inflated membrane. The fabric is made in a plant where the people are doing the best they can, but people are also not perfect.
Some fabrics will have stretch problems that have gone unnoticed; some will have other factors. After the membrane is manufactured, it is then attached to a foundation and inflated. Here again, the people making the foundation can make mistakes. These mistakes can be serious and can change the shape of the dome. The contractors in the field that build the Monolithic Dome can also affect the shape of the profile and on large domes, they can drastically affect it.
With the profile shape being affected by the membrane’s fabric properties, the manufacture of the fabric, the inflation method, the foundation and the actual construction, it is too easy to have small variations in the inflated shape that can have a huge impact on the construction of the building.
In dome building using an inflated form, it is extremely important that the spherical shape of the structure be exactly that spherical shape and it also is extremely important for this spherical shape be consistent. For instance, it is possible to change the shape dramatically during construction. The buildings built need to be profiled after they are constructed. We have profiled hundreds of buildings and find that they all have variation. Some of the variations are small, others have large variations. What causes these variations? In most cases it is the actual construction.
After the Airform membrane is inflated, a primer is applied to make the polyurethane foam stick better, then polyurethane foam is applied. The polyurethane foam should be applied uniformly, but this is nearly impossible. It can be applied thin or thick — thin in some areas, thick in other areas. This polyurethane foam has an enormous amount of pull and can actually change the shape of the membrane by how it is applied.
But nothing can change the shape as much as the application of the concrete.
Concrete is shot in place. If too thin in one area and too thick in another it will also change the shape of the dome profile. These changes are generally not a problem if caught and fixed early on. But, if overlooked, they can be very much a problem.
The danger of the small variations caused by all of the above is greatly increased as the shape of the finished domes are started out close to the maximums.
In other words, it is easy to draw a specific curve on a blueprint. If that line is critical and changed by any of the above, the results of the finished dome can very serious. These problems may not show up for days, months, even years, or perhaps decades, but they will show up eventually.
So why take the chance?
We are starting to see dome designs and engineering that lower — flatten — the shape of the dome. They are particularly interested in square-looking buildings. They want to build a side wall on the school building and then put an extremely low-profile dome across it. They think the low-profile dome is prettier, less obtrusive, and they hide it this way to make the building more conventional looking.
The problem is, if you lower the dome profile too much you end up with some serious risks, you lose some serious benefits and you increase your costs unnecessarily.
The shell of the Monolithic Dome is extremely strong, far stronger than most even engineers understand. But it is made by inflating a membrane, then spraying the primer, the foam and finally, spraying the concrete. If you know much about concrete you know that concrete does not instantly have all of its strength.
In fact, we test concrete often times at three days and then thirty days, and in some cases we take sixty days. It will have increased strength by then immensely. This means it can also sag and move in the first few hours or days.
It doesn’t make sense to take the chances and risk the safety of the buildings and the people in the buildings. It is unnecessary and could be considered unethical and irresponsible.
As a rule of thumb use a minimum ratio of 1 to 5 of height to diameter for the profile. As the ratio goes up to 1 to 8, the costs go up markedly as well as the risks. In general, the cost will be at a minimum from 1 to 4 and 1 to 5. So why increase the risk? This is especially true of large diameter structures.Never push the margins by dropping the profile below the 1 to 5 profile. Remember to always design for safer buildings.
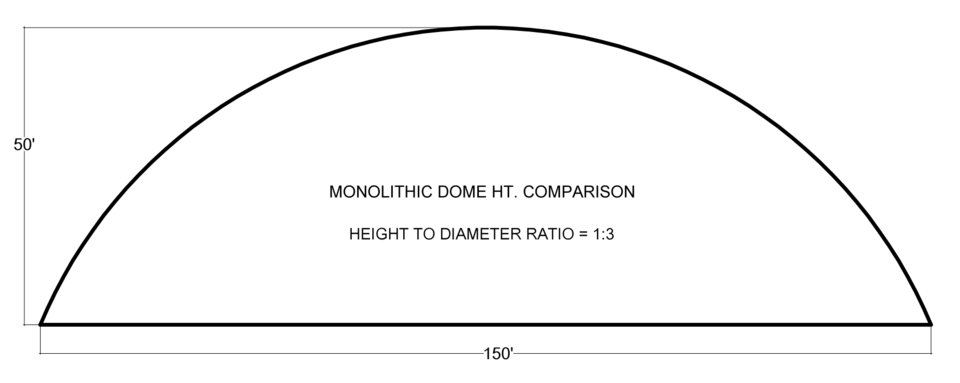
DOME PROFILE 1:3 – This profile has a height a third the length of the diameter. The 1:3 profile shown here is 150’ wide and 50’ tall. This profile makes a spectacular arena. A second floor is possible with this profile and the walls are close enough to vertical, you don’t lose much space around the perimeter. Most important is the fact that the surface area is quite large. Surface area is like a battery and what helps hold the cost of heating and cooling down in a Monolithic Dome.
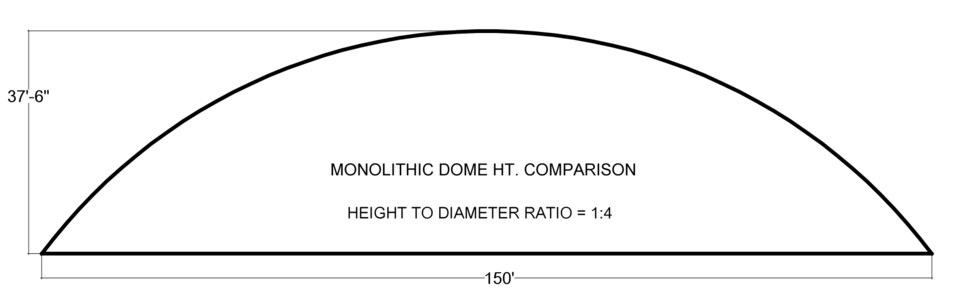
DOME PROFILE 1:4 – If we go to a 1:4 ratio, in this case a dome with a 150’ diameter and height of 37.5’, we have the least expensive roof to put over that much floor area. There is still enough height that for many buildings, there is walking space around the perimeter. The 1:4 profile gives you the most bang for your buck with the large surface area acting as a thermal battery.
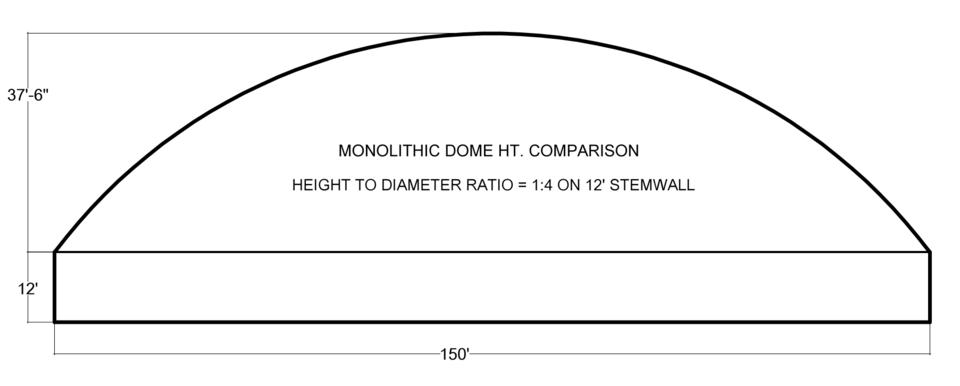
DOME PROFILE 1:4 on Stemwall – The 1:4 dome profile can also be built on a stemwall for a more conventional appearance.That thermal battery is extremely important and even though it rises higher than some buildings, it works and works well.
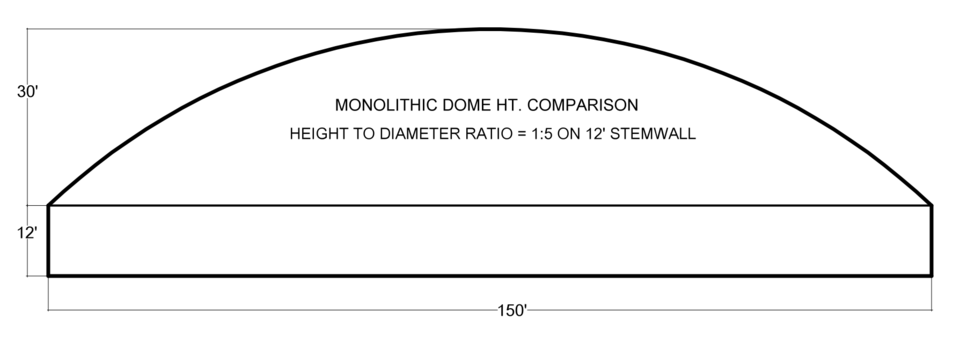
DOME PROFILE 1:5 on Stemwall – The 1:5 ratio dome is low enough profile it probably needs to be on a stem wall. The stem wall can be as low as nine or ten feet or it can be as high as forty or fifty feet. The stem wall is important to some architects and some owners, although it is an expensive way to get height. However, the 1:5 ratio on a 12’ stem wall makes an extremely good basketball facility, hockey stadium or small arena. The surface area of the roof is still large enough to make that all-important thermal battery.
(Note – A 1:5 ratio and a 1:4 ratio covers the same amount of floor area for the same amount of money. They both work.)
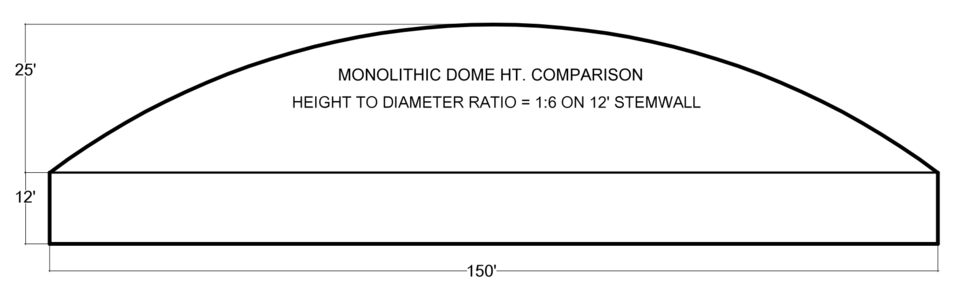
DOME PROFILE 1:6 on Stemwall – The 1:6 ratios shown here has a diameter of 150’, dome height of 25’ on a 12’ stemwall. This ratio increases the outward thrust at the edge of the dome which increases the pressures and the chance of distortion. At 1:6, we move into dangerous construction, especially when using an air-formed membrane.
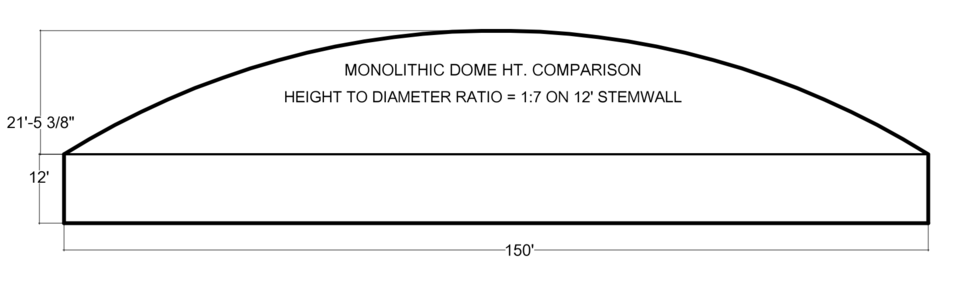
DOME PROFILE 1:7 on Stemwall – We are even further into the dangerous construction ratios at 1:7. The 1:7 ratio shown here has a diameter of 150’, dome height of approximately 21.5’ on a 12’ stemwall. The air-formed dome is sprayed in place and I don’t care how careful the sprayers are, they can tend to distort that shape. If that shape is distorted the strength of the building is compromised considerably.
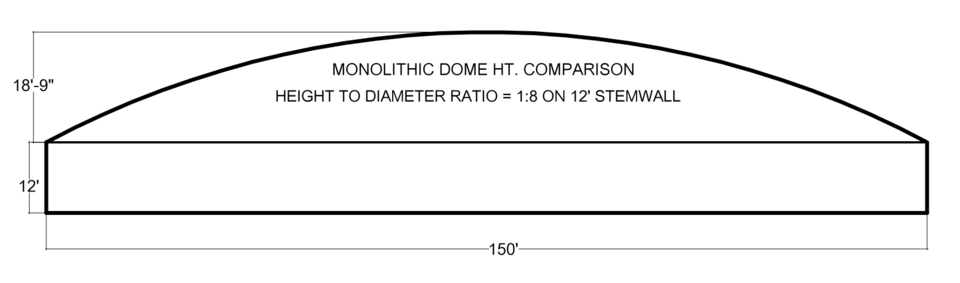
DOME PROFILE 1:8 on Stemwall – At 1:8, construction becomes extremely dangerous. The 1:8 ratio is pure foolishness. It works where non air-forming is done because the application of the concrete is not going to be a big deal in the shape, but with the air-forming it is a big deal and it is extremely important not to play with it.
(Remember, as the side thrust goes up, the pressures go up and the chance of distortion goes way up.)