Editor’s Note: Monoform Primer is now marketed as Bayblock Prime FR.
Why the Monolithic Airform makes the best roofing membrane
History
When we built the first Monolithic Domes, the Airforms seemed terribly expensive. We decided to use the Airform as a tool, rather than a permanent part of the building. We would inflate the Airform, spray the underside with three inches of polyurethane foam, tie the rebar, spray the concrete, peel the Airform and coat the exterior foam with roof coatings.
Roof coatings are a major subject unto themselves, but it is simply a way of protecting the foam from degrading sunshine. There are literally thousands of roof coatings – most of which have a very short life. Any time a roof coating fails, trouble begins.
More than 50% of complaints owners have about buildings are associated with leaking roofs. It is paramount a roof be built in such a way that it will not leak. Coatings must not fail and leave the urethane exposed.
Early Monolithic Domes were coated utilizing various materials such as stucco, acrylic elastomers, butyl rubber elastomers and urethane elastomers. I was so paranoid about vandals damaging the exterior foam that for the first several domes we sprayed the exterior’s bottom ten feet with two inches of concrete. From all of the above experiments, I learned many valuable lessons.
Lesson #1: Primers on the Airform
If you want something to stick to the Airform, you need to use a primer! The primer does two things. Firstly, it locks the plasticizers into the Airform. The Airform is made from PVC which is a hard substance. Chemicals are added to make it flexible. Over time these additives dry out or migrate out of the fabric. That migration can damage a coating and cut the Airform’s lifetime.
Secondly, the primer acts as a glue to insure the bond of the coating or urethane foam to the Airform. Pretreating the Airform with Monoform Primer is an absolute must! It can be applied with an airless paint gun or rolled over the Airform’s exterior or interior. A thin layer is all that is needed (300+ sf per gallon). Let the primer dry completely before applying another coating.
A primer is not needed under metal cladding or chain-shell.
NOTE: Some urethane base coatings can be used on the Airform’s exterior without the need of a primer.
Lesson #2: Vapor Drive and Blisters
When the Airform has been removed, most coatings on the exterior of a dome’s polyurethane foam will not last more than five years. As coatings degrade, sunshine drives vapor into the foam. Vapor condenses within the foam structure, then expands under more sunshine and creates blisters. As blisters grow in number, they become almost impossible to deal with. In time the foam and coatings totally fail and the dome leaks.
Lesson #3: Coatings
There are coatings that will hold up for many years, but if used on a dome without an Airform they can be very expensive. In the long run and in all cases, coatings that withstand vapor pressure, sunshine and real world use will cost far more than simply leaving the Airform on. Successful coatings are generally two-component urethanes that are expensive to purchase and to apply. However, they do work.
Lesson #4: Coating application over the Airform
Elastomeric Coating – It’s extremely easy and inexpensive to “paint” an elastomeric coating over an Airform’s exterior. An elastomeric coating is a stretchy paint. There are many formulations, some better than others.
Simply put, it’s a coating of “paint” over the exterior that replaces the plastic burned off by the sun. The coating can be colored and provide a new surface.
Generally, one gallon per 100 square feet will do the job if the base fabric has not been left too long. Using a primer on the Airform is required before coating. It locks in the plasticizers of the Airform and insures adhesion of the coating.
Acrylic Stucco – It’s another good coating option. The product selected must be rated for more than vertical surfaces. Most have the advantage of being thick. Wrinkles can be “battered” out before it is applied, thus leaving a very even stucco finish.
The stucco can be applied with a roller, a brush, a squeegee, a drywall hopper gun, a sand pump and more. Acrylic stucco can be applied immediately upon the finish of the dome. Colorant can be mixed into many of these stuccoes and provide varied surfaces. They can be heavily textured. Again, Monoform Primer should be used to lock in the plasticize and insure adhesion.
The question then becomes: Is it cheaper to peel off the Airform and apply a coating that costs as much or more than the Airform so we can save the Airform for an additional use – or – is it more economical to leave the Airform on?
Lesson #5: Airform Damage
Multiple uses of the Airform damages it. Polyurethane, as it attaches itself to the underside of the Airform, pulls some of the plasticizers out of the fabric. After a few uses, the Airform becomes very brittle, susceptible to tearing and very difficult to work with.
We’ve built as many as twenty buildings with one Airform, but at the end of the twenty buildings the Airform was shot. As the Airform degrades from multiple uses, it becomes riskier to use and has a greater chance of splitting.
Lesson #6: Mold Release
About this time, somebody says, “Let’s use a mold release on the Airform and then it will peel off easily.” The bottom line is: If it peels before the structure is done you’ll probably kill someone. The Airform must be firmly adhered at all times, or the structure will collapse within the Airform.
This is one of my biggest fears with EcoShell II construction. It is possible for the Airform to release before the structure is completed. This means a super good adhesive/primer must be used to insure adhesion to the Airform during the construction process. Then when the Airform is peeled off, the bond between primer and Airform is broken. How much damage is caused to the Airform is still unknown. It certainly does some damage. Would it allow us to use the Airform 100 times? I’m not sure. It might. It might be a lot less.
The EcoShell I Airform does not have any adherence to shotcrete; therefore it falls away to the interior with very little stress. That is why we can easily get 100 uses from an EcoShell I Airform.
Lesson #7: Airform Storage
We peeled off the Airform on the first 100 domes we built. It is amazing how many times we ended up storing an Airform and never using it again. Storing the Airform becomes a problem. The Airform never folds into the nice little neat package that it did when it was new, so we wind up with a huge Airform stored someplace where it might get burned or where rodents can get into it. It can also be damaged by handling, not to mention the capital cost of stored Airforms.
So, to recap, the Airforms can be used multiple times, but good coatings cost as much as Airforms, so we wind up with an Airform that we paid for in addition to the coating cost. In effect, we doubled our exterior cost because we have tried to save the Airform for the second, third, fourth or tenth use. Unless we can get those ten uses, we certainly go backward.
Lesson #8: Metal Cladding
During the time period when we removed Airforms for reuse, we tried many different coatings. We used asphalt emulsions, acrylic elastomers and many others. We sprayed the bottom ten feet of the dome with two inches of concrete to protect the dome from vandals.
Over ten years, all but a few of these coatings failed. Blistering and foam problems were evident. Those customers looked to us to solve the roofing problems. Foaming or coating over a failed foam roof has seeds of disaster written all over it. Water is generally trapped in the failed roof due to vapor drive. If we put a new roof over it, we trap the water within. It expands creating more new blisters. What a mess!
To solve the problem we developed a method using metal cladding over the exterior. Metal cladding protects the foam from sunshine, protects the building from rain, yet allows the moisture under the metal shingles to escape since air can move under the shingles and carry off the water vapor. This is the only successful method we have found for repairing a failed foam roof. Metal cladding creates a different look to the structure. It is a nice solution in many cases. Remember, a primer is not needed under metal cladding.
Lesson #9: Removing concrete from the exterior of a dome that has had the Airform removed
The removal of concrete that had been applied directly to the foam unveiled yet another surprise. Concrete on the exterior moves at a vastly different rate than concrete on the interior. Interior concrete is insulated from the real world; therefore it stays constant in temperature and size.
Exterior concrete, however, is not thermally protected so it expands and contracts and seriously moves. It moves from summer to winter and from freeze to thaw. When concrete is applied directly to urethane foam, it firmly adheres to the urethane, cracks and propagates those cracks through the foam to the concrete shell below. As those cracks occur, leaking begins.
Would that happen in the tropics? I’m not sure because I didn’t spray any building exteriors in the tropics. I have sprayed buildings as far south as Tulsa, Oklahoma. In that case, the concrete caused the failure of the foam underneath and then the building leaked.
Could that have been prevented with a coating underneath the concrete over the foam? Perhaps, if it was a very good coating. Asphalt emulsion we used on some buildings did not work; acrylics used on other buildings didn’t work. Maybe a good urethane elastomer would have worked, but it is costly.
Lesson #10: Airform as a Vapor Barrier
The next surprise came when we stripped the concrete off the domes’ lower portion. The urethane foam was saturated with water. Urethane foam is tough to saturate. Free water will not enter urethane. Only water vapor saturates urethane. There is a condition that is set up by the exterior covering of concrete where water that gets behind it is driven by solar pressure that creates a vapor drive and drives water into the foam.
We’re not talking small amounts of water. When we used a backhoe to strip off this concrete, we found saturated foam. As the backhoe squeezed the urethane, it released large amounts of water. Any block of urethane could be squeezed, making water pour as if squeezed from a sponge. This water can only enter via a vapor drive.
You can put a block of urethane in water and keep it there for years and it will not absorb enough water to even be measured. I have a block of urethane in a container of water that I have kept there since 1970. It has not absorbed any moisture that can be detected. Therefore, we learned that concrete over foam will not protect the foam from vapor drive. It takes a vapor barrier such as an Airform to protect the foam.
Lesson #11: Chain-Shell, Chain-Link Reinforcement and Stucco
To expect an exterior covering of concrete over urethane to work, there must be a covering between the two that protects the urethane from vapor drive. We know of nothing that works better than an Airform. It has the strength to withstand the movement of exterior concrete. It’s not important for the exterior concrete to adhere to it. Therefore the concrete can give and take without damaging the foam beneath. Shotcrete is an excellent exterior coating over the Airform if it has a chain-link fence embedded in it.
Often, we have people suggest that we use chicken wire for exterior reinforcing. Chicken wire would be great if it would wrap neatly around the ball – but it doesn’t.
Chain-link fencing forms to the dome. It’s made of galvanized steel, so it won’t rust. Chain-link fence provides just enough reinforcing to prevent any gross movement of exterior concrete. Exterior concrete will, in fact, expand, contract and crack. It has no choice. It is laying over an immovable object, i.e. the Monolithic Dome.
So, how do we apply the exterior concrete so that it doesn’t look like a cracked-up mess after it’s been on a few years? Stucco has been utilized for many years. Stucco applicators have learned a few things from experience. First, concrete cracks. It needs to be applied in layers. Remember, a primer is not needed under chain -shell.
Standard stucco is done by applying a scratch coat, a brown coat and a finish coat. The scratch coat is approximately 2/3 of the thickness and left rough (often scratched to be very rough) and alone for three to six weeks to allow it to cure and crack.
The brown coat is next applied over the scratch coat. It consists of about another third of the total thickness. It fills the cracks left in the scratch coat. It is also left for three to six weeks. The brown coat also cracks, but because it is over a much stronger scratch coat the cracks are generally much smaller. After the brown coat cures there are more cracks, but smaller ones.
The finish coat is then applied over the brown coat at the end of its three- to six-week cure. The finish coat will then have much finer cracks which are barely noticeable. The finish coat can have acrylic mixed with it, minimizing the size of the final cracks. The above method is the best method for applying concrete to the exterior of an Airform.
Why would we want to apply concrete to the exterior of an Airform anyway? It creates a permanent exterior. It costs a bit more than an acrylic coating, but it will withstand far greater physical damage, including serious fire and abuse from physical objects such as super large hail stones.
Lesson #12: Ceramic Tile and Miscellaneous Coverings
Ceramic tile has been used for years as an exterior covering on a variety of buildings and many Mosques throughout the world. The key here is to install the ceramic tile before the Airform gets in trouble, since tile becomes more cohesive from the strength of the Airform.
Another effective protection for the dome is brick, other manmade tiles, or concrete tiles.
Rock is a good, non-ablative material. Flagstone has been used on a few Monolithic Domes. Although we have seen satisfactory jobs where the stone had been laid right against the Airform itself, we suggest covering the dome with chain-link and a layer of concrete before the flagstones are set.
Lesson #13: Monolithic Domes vs. EcoShells and Concrete/Foam/Concrete Sandwiches
During MDI Workshops, we discuss the current state of construction. We don’t have time to discuss all the blind alleys and ways of doing things that we have tried which didn’t work. Many times dome enthusiasts think that we have just not thought of this “new idea.” It is not so; we probably have thought of and tried the “new idea,” but rejected it simply because it just didn’t work.
Many people talk to me about inflating an Airform and applying a layer of concrete on the inside, similar to EcoShell construction, then applying a layer of urethane, then another layer of reinforced concrete to provide the actual structure of a Monolithic Dome. So we wind up with this concrete sandwich. Then they want to peel the Airform from the outside and reuse it. I say no! The reasons for saying no are in the above discussion.
Number 1 – The adherence of a layer of concrete to the Airform is much trickier than urethane, and in cold weather it is just out of the question.
Number 2 – We have a concrete-foam-concrete sandwich that is destined to crack and leak. There is no protection for the urethane from vapor drive from the outside. The building, in our experience, will leak. No doubt about it – none whatsoever! It may not leak the first year or even the first ten years, but it will eventually crack and leak.
Building in this manner generates a smoother exterior – that is granted. However, most of our customers prefer the stucco look. Lastly, it costs more money to build this way, so why in the world attempt an inferior method that has been checked, verified and experimented with over the years and wind up with an inferior product?
Turning an EcoShell into a Monolithic Dome will cost more and create more trouble than it solves.
The Bottom Line
Don’t peel your Airform. It protects the foam from Vapor Drive and the elements. Wash it to keep it looking new.
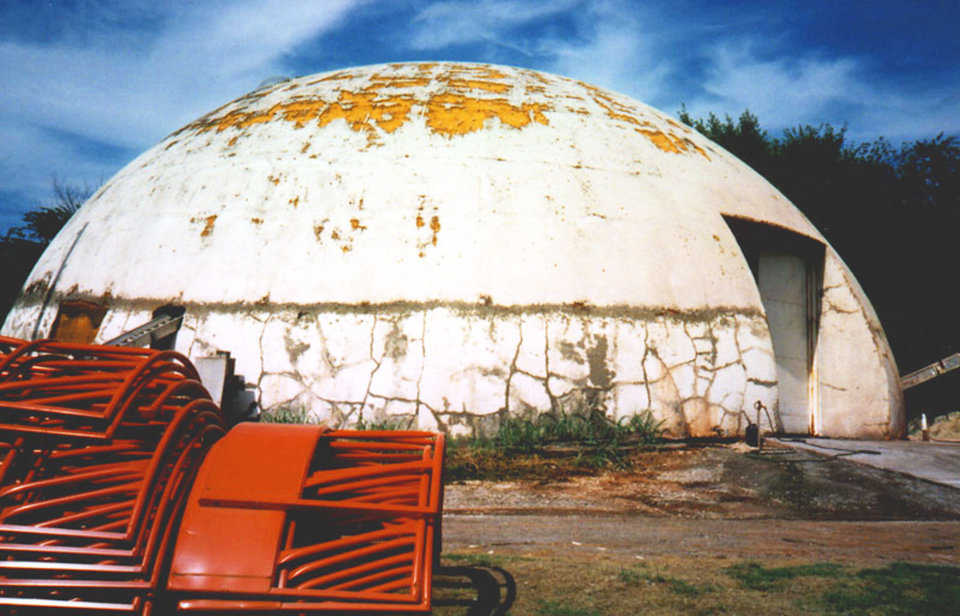
Vapor Blisters — One of the early domes where the Airform was removed. Because the coating is in bad shape, the dome needs recoating or metal cladding – Chandler, Oklahoma.
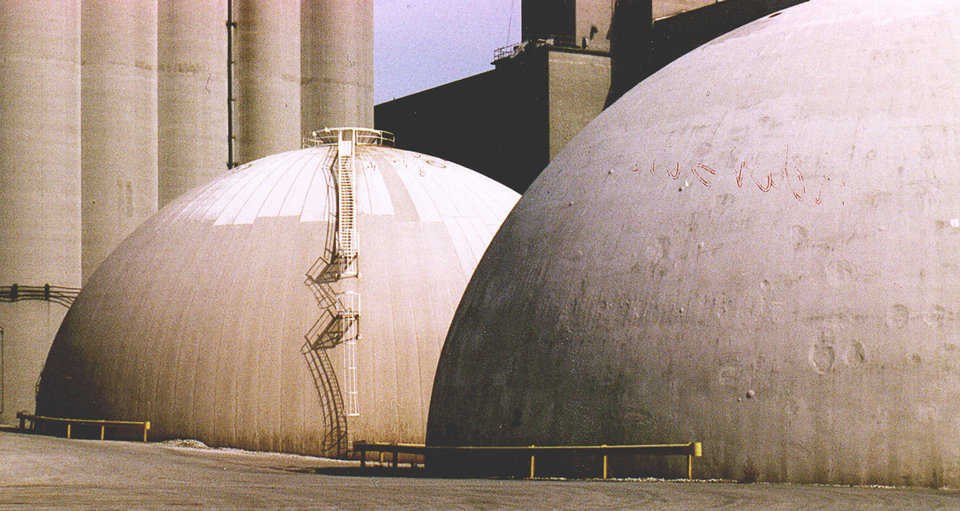
Anderson’s Grain Storage — The building on the left is ready for recoating. It cannot be let go any longer or the Airform will delaminate and come off. The building on the right was let go to the point where the Airform had to be stripped. It has been recoated, but it will never be as good as it would have been had it been coated before the Airform had disintegrated.
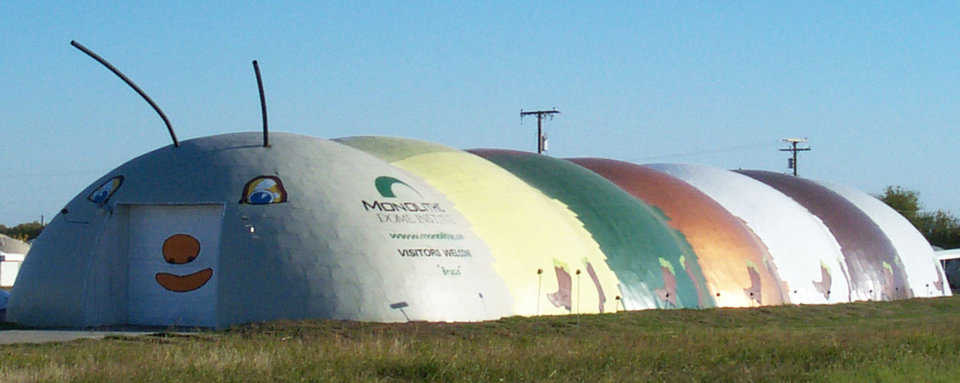
Bruco — Bruco, The Texas Italian Caterpillar in Italy, Texas (Monolithic Airform Manufacturing) was completely covered in metal cladding in 2001.
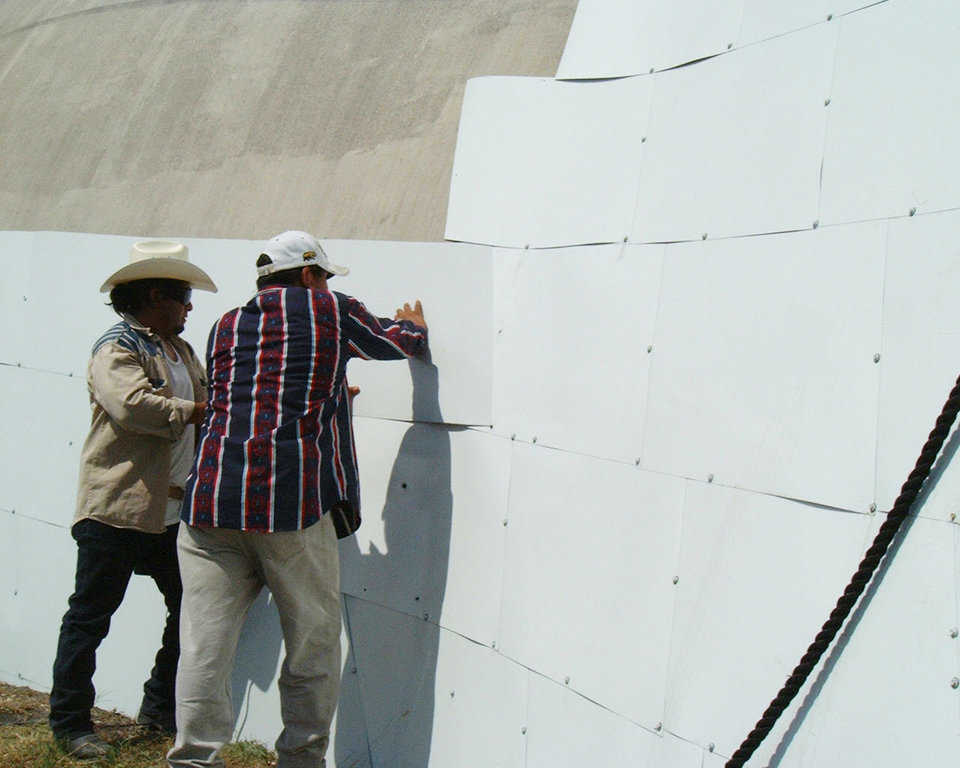
Metal Cladding — Application of metal cladding on Bruco in Italy, Texas. Metal Cladding is metal plates similar to shingles fastened to each other and the dome with mechanical fasteners. Metal cladding is especially useful for the dome built without the Airform or to cover a dome with Airform difficulties.
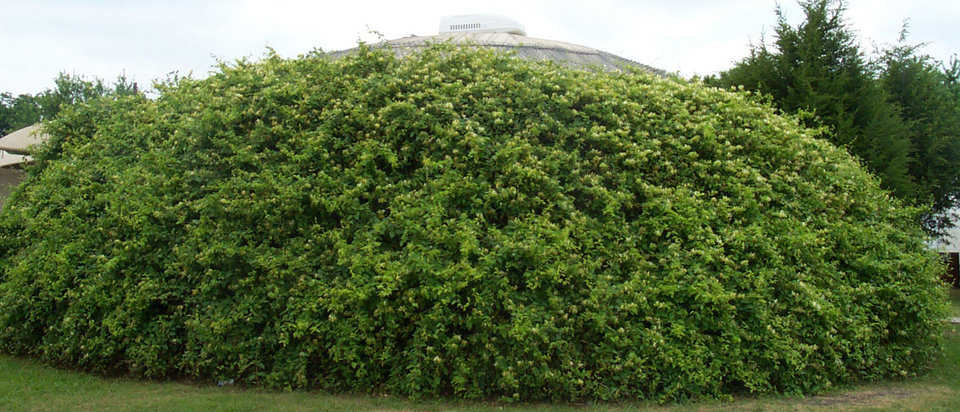
Honeysuckle Wall — The outer layer of Airform is PVC plastic. At Monolithic, we have one dome with chain-link fencing attached to the outside and honeysuckle climbing on it. In five years we have not noticed any deterioration of the vinyl. Generally, plants keep the dome cooler and protect the dome skin from harsh ultraviolet rays.
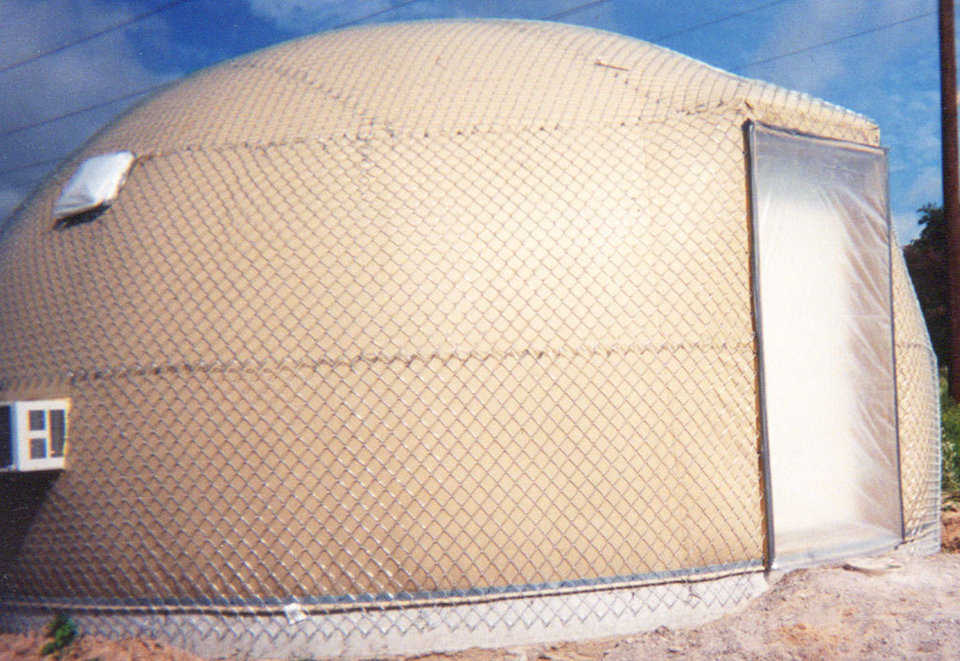
Chainshell — This dome is ready to be sprayed with shotcrete. Chainlink fence is galvanized and easily conforms to the shape of the dome.
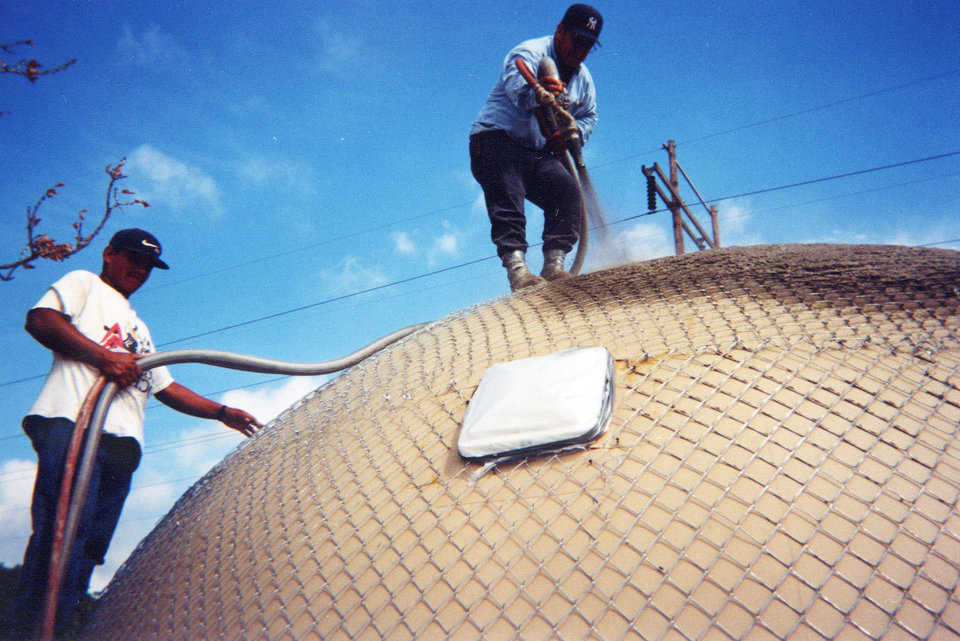
Applying Shotcrete — Javier and another Monolithic crew member are applying the first layer of shotcrete to the exterior of the dome. This layer will be followed with two more, much thinner, layers.

Bounceback Coating — Application of a beige Bouncback coating. Bounceback is a product of UCSC.
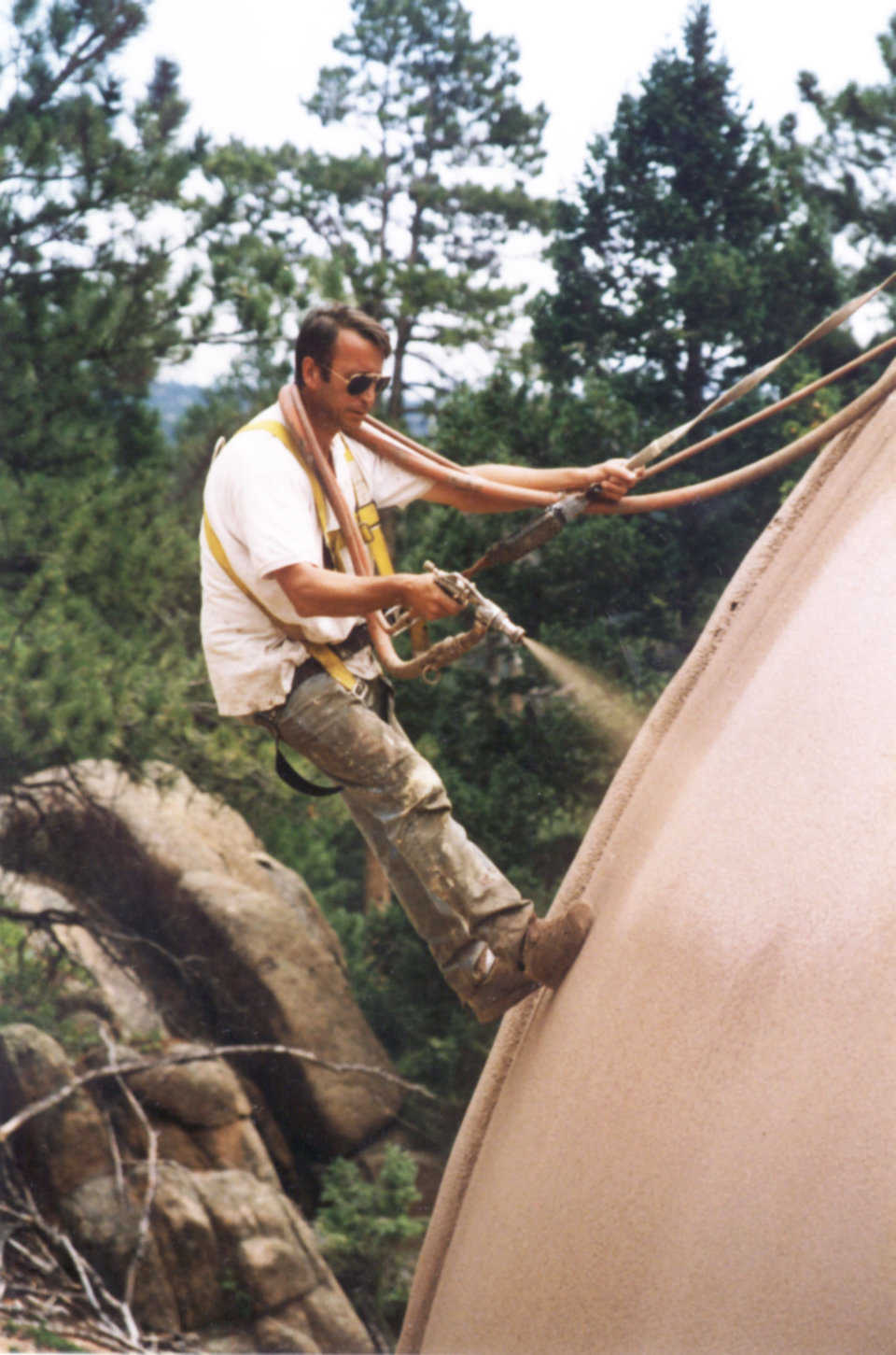
What A Job — UCSC spraying coating to dome exterior. Photo courtesy UCSC.