Grain Covers for storage are made better than ever with Monolithic’s RF welder.
A Superior RF Welder that Makes Superior Grain Covers
“Monolithic has one of the largest radio frequency or RF welders in the world,” said David B. South, Monolithic’s president. "An RF welder produces heat and fuses materials with radio frequency energy, akin to microwave energy. The result is a weld that is every bit as strong as the original material.
“In other words,” David continued, “when two sections of fabric are fused with an RF welder, it’s like the weld doesn’t even exist – like it’s just one, much bigger piece. We’ve been using this machine since August 2001, when we installed it in Bruco, our Airform manufacturing plant.”
According to Don Garrison, Manager of Monolithic’s Airform Division, the welder can handle a greater variety of fabrics, in both weight and size, including fabrics with a width of 126 inches. “With this welder we build Airforms used in the construction of Monolithic Domes, and we make a variety of other products, including grain covers. We can design and make grain covers that can literally stretch over acres of ground,” Don said.
“The RF welder has a couple of other advantages as well,” he added. “It produces a better weld because it can sense any variation in the thickness of the fabric, and it’s laser guided. Laser beams stretch down the table so you can see precisely where the welder is going to hit.”
Protecting a Harvest
That’s a major concern of large, grain growing corporations as well as small, independent farmers.
David South said, “Stored crops must be shielded from the sun, moisture, wind, birds, rodents and insects. Because of the fabric and construction process we use, Monolithic grain covers do that. The customer tells us how big the grain pile is going to be, and we build the cover – usually with a diameter ranging between 150 to 350 feet. We use the same tough, polyester fabric that we use for our dome Airforms, but in a lighter weight and always white since white reflects sunlight.”
Monolithic usually designs its grain covers in eight to twenty sections, each weighing about 1000 pounds or about the maximum weight that a crew can handle.
“Often,” David said, “those covers are so large they are shipped in pieces, then bolted together by the customer, at the worksite. Some enclose grain piles that are more than 300 feet in diameter and 70 feet high – or an area of 1 1/2 acres.”
In the field, these sections must fit and fasten together to effectively protect the stored grain, sometimes for six or seven months. This is done by laying the sections against each other, turning the edges vertically, laying a cap strip, then placing grommets spaced 18 inches apart. The turned-up edges prevent rain water from seeping into the grain pile. Instead, it runs off the grain cover.
“Rain is the number one problem,” David said. “But the turned up edges and the cap strip create a little roof over the joint and that keeps the rain out.”
Grain piles are provided with air pipes running through them and fans stationed around their perimeters. In calm weather, the fans blow air through the pipes and into the grain pile, driving off excess moisture and heat.
But during high winds, that action is reversed. Instead of blowing, the fans suction air out of the grain pile, making the cover fit down tightly over the grain and preventing the cover from blowing away.
Usually, a wooden fence, about eight feet high, encloses the grain storage area. A tubelike tower, with a lifting ring that can slide up and down the tower, stands in the center of the grain cover. The middle of the grain cover fits around the tower, while its bottom is secured to the fence.
Grain is conveyed to the top of the tower via a conveyor, then dropped down the tower. As grain begins piling under the fabric cover, the lifting ring lifts it. When the fabric reaches its capacity, a cover is fastened over its central opening. Result: A cone-shaped, fabric structure full of protected, stored grain.
When it’s time to unload the grain, workers unbolt one or two cover sections at a time, roll them up and put them in storage. They then gather the grain with a front-end loader.
Don Garrison said, “The life of a grain cover really depends on what it’s exposed to, but most last about seven years. Large grain growers usually have a replacement schedule; they replace a certain number of sections every four years.”
What Customers Say
The Andersons, Inc., a diversified agribusiness with grain elevators in Ohio, Michigan, Indiana and Illinois, has been a Monolithic client for both domes and grain covers for more than a decade.
Operations Manager Bob Marlow, who has a 30-year employment history with The Andersons, oversees the company’s facility in Delphi, Indiana. Built in 1975, Delphi ordered its first grain cover, a Monolithic product with a diameter of 320 feet, in 1993.
According to Marlow, this grain pile was actually put in to handle overflow. “But over the years,” he said, “it evolved, so today it’s not used for overflow, but for what I consider our working space. We used to fill it when other areas were full. Now we do it as a matter of business. Part of that is because compared to a fixed storage, the cost of a grain pile is relatively cheap.”
Marlow calls this type of grain pile “cover-on-first technology” since the grain cover is in place before grain is poured under it. Consequently, the grain is never exposed to the environment. He explained that Delphi’s grain cover is a large diameter, round tarp with a lifting pipe at its center. Shelled corn, some 1.8 million bushels of it, flows through that pipe and forms a cone-shaped pile beneath the grain cover.
Delphi usually fills its grain pile in October and empties it in May. Marlow said, “Typically, from this facility, the corn goes to poultry feeders or corn processing plants where they produce corn syrup.” While this hard kernel corn is not the kind that usually finds its way to our dinner tables, much of it is ground and made into corn chips.
Marlow said that during storage a system of 16 fans and aeration tubes serves two important purposes: maintaining the quality of the grain and keeping the tarp in place. “It’s all downward drafts,” he said, “so it pulls the tarp down over the corn.”
Since its installation, sections of Delphi’s grain cover have been replaced. “But we still use two of the original sections. The product has served us well,” Marlow said.
Johnson System, Inc., a company that designs permanent and temporary grain storage systems for major co-ops and elevators, such as Central States Enterprises, has also purchased Monolithic grain covers.
President Howard Johnson said that Monolithic products are often used in what the company calls its Quality Pile System, round units with a seven- to ten-year lifespan. They have a 500,000 to 3,000,000 bushel capacity, use bolt-up tarps that are electrically winched and have a tunnel reclaim system.
In addition, Johnson’s Standard Pile System often includes pull-over tarps manufactured by Monolithic, that are installed after filling.
Asked about product satisfaction, Johnson said, “You folks (Monolithic) produce a high quality, longer life type of tarp. We like it.”
Originally published March 22, 2007
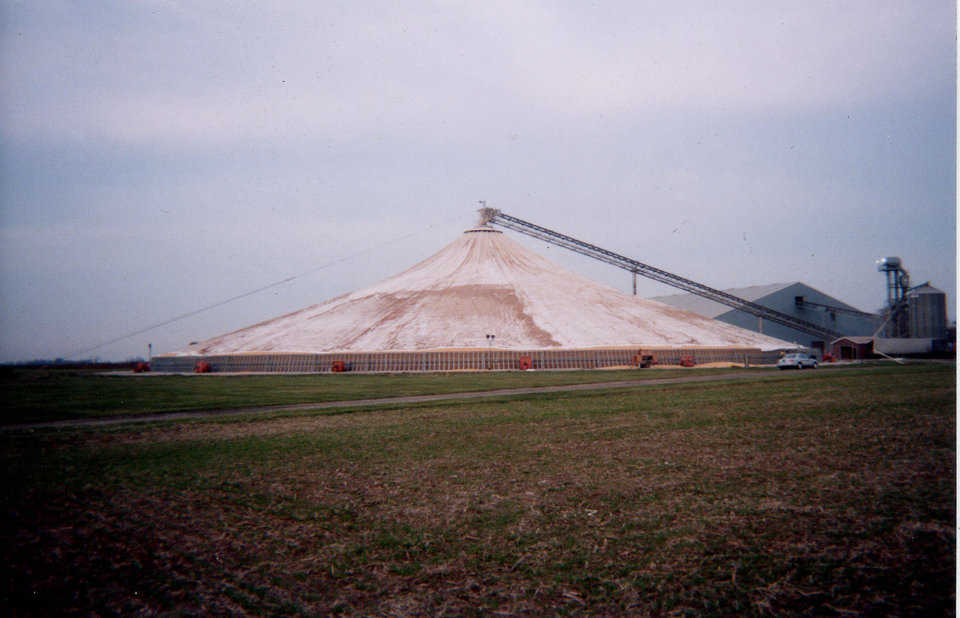
Grain is conveyed to the top of the tower via a conveyor, then dropped down the tower. As grain begins piling under the fabric cover, the lifting ring lifts it. When the fabric reaches its capacity, a cover is fastened over its central opening. Result: A cone-shaped, fabric structure full of protected, stored grain.
Airform fabric inside Bruco, our Airform manufacturing warehouse that houses our radio frequency welder.