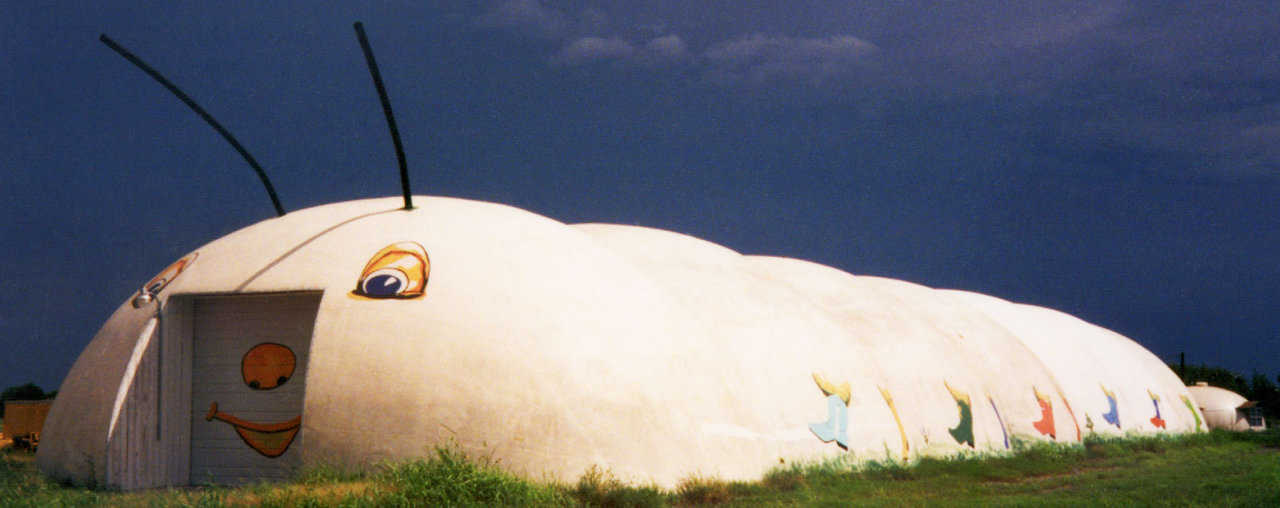
Bruco, our Texas Italian Caterpillar — Bruco’s 7, 60-foot, interconnected domes make a 14,000-square-feet factory with computers, cutting tables and machines for the design and manufacture of Airforms and various types of liners and covers. The overall size is 60’ wide by 240’ long by 20’ tall.
Bruco – A Very Busy Caterpillar
Not a typical factory
With its flirty eyes, smiley mouth and cowboy boots that glow in the dark, Bruco, our manufacturing plant in Italy, Texas, looks nothing like a typical factory. But while Bruco might look like a playful, giant caterpillar on the outside, it’s serious work on the inside.
Bruco’s seven, 60-foot, interconnected domes encompass 14,000 square feet of factory space that houses computers, cutting tables and several kinds of machines.
Moreover, inside Bruco, Monolithic Airforms, a subsidiary of Monolithic Constructors, Inc., can design and manufacture an Airform large enough for a 300-foot diameter Monolithic Dome, a 1,000-foot diameter Crenosphere, or a grain tarp to cover a two-acre grain pile.
State-of-the-art
Two things make the manufacture of such enormous fabric structures possible:
- Bruco’s size: 240′ × 60′
- Cutting-edge technology
David South, president of Monolithic, said, "In 2001, we installed a very impressive, new machine. It is an automated, laser guided, 200-foot long welder, that can heat and seal fabric pieces with microwave.
“We have one of the largest machines of this type anywhere, allowing us to build super-big, fabric structures – tarps, Airforms or whatever.”
Airforms and more
While the manufacture of Airforms for domes is still the major part of what goes on inside Bruco, other fabric structures are also made.
South said, “We build a lot of tarps. Many are just like a flat sheet that might be used to cover a tennis court. But many are quite specialized. These include grain covers, condensate ceilings, membranes for methane storage tanks, diaphragms for water tanks, tension tarps and pond liners.”
Grain Covers
Protecting their harvest is a major concern of large, grain growing corporations as well as small, independent farmers.
South said, "Customers, who store huge piles of grain outside, must keep it out of the wind, rain and sun. So they cover it with a cone-shaped, fabric tarp. The customer tells us how big the grain pile is going to be and we build the cover. We use the same tough, polyester fabric that we use for our dome Airforms, but in a lighter weight and always white since white reflects sunlight.
“Often,” South continued, “those covers are so large they are shipped in pieces – 12 to 15 pieces that are bolted together by the customer in the field. Some enclose piles 300 feet in diameter and 70 feet high – or an area of 1 1/2 acres.”
Usually, a wooden fence, about four feet high encloses the grain storage area. A tower topped by a head house, stands in the center of the fenced area. The middle of the grain cover fits around the tower, while its bottom is secured to the fence.
As grain begins piling under it, the cover rises, ultimately creating a cone-shaped, fabric structure. Blowers connected to the structure pump fresh air under it in calm weather. But if a storm arises, the blowers suck out the air and make the tarp into a tight shield over the grain.
Don Garrison, manager of Monolithic Airforms Manufacturing, said, “The life of a tarp really depends on what it’s exposed to, but most last about seven years. Large grain growers usually have a replacement schedule – they replace a certain number of sections every four years.”
Johnson System, Inc., a company that designs permanent and temporary grain storage systems for major co-ops and elevators, such as Central States Enterprises, has also purchased Monolithic grain covers. President Howard Johnson said that Monolithic products are often used in what the company calls its Quality Pile System, round units with a seven- to ten-year life span. They have a 500,000 to 3,000,000 bushel capacity, use bolt-up tarps that are electrically winched and have a tunnel reclaim system.
In addition, Johnson’s Standard Pile System often includes pull-over tarps manufactured by Monolithic, that are installed after filling.
Asked about product satisfaction, Johnson said, “You folks (Monolithic) produce a high quality, longer life type of tarp. We like it.”
Condensate Ceilings
Communities that use elevated, steel water tanks sometimes build the tanks over offices or equipment storage sheds.
“So they need a condensate ceiling to fit under the tank,” South said. “Moisture forms on the outside of the tank and drips down. The condensate ceiling, made of our polyester fabric, acts like a diaper that collects the liquid. It’s cut to an exact size and attached under the tank with special hooks. You can’t see it because it’s covered by a metal skirt over the tank’s legs. We make a lot of those each year for several companies.”
Methane Storage Tank Membranes
Some sewage treatment plants use huge concrete tanks, sometimes lined with rocks, into which raw sewage is pumped. Bacteria living in the tanks digest the sewage and, in the process, produce methane. If treated properly, that methane can be used to run generators. But if not treated properly, obnoxious odors and an unclean atmosphere will develop.
At Bruco, Monolithic Airforms manufactures membranes for methane storage tanks. Two such membranes, an outer one that is always kept inflated and an inner one that rises and falls depending on the amount of methane under it, effectively control the odor and protect the environment.
Water Tank Diaphragms
“Approximately one of every 50 large, multistory office buildings in the U.S. has a water thermal storage system,” South said.
North Park Central in Dallas is one such facility. It has two huge water thermal storage tanks, each with a diaphragm manufactured by Monolithic Airforms. The diaphragms are designed and shaped so that they can rise to the top of the tank or sink to its bottom, depending on the temperature of the water.
“Water has a property called thermocline,” South explained. "That means that water stays in temperature layers, with the warmest at the top. So during the day as the tank fills with warm water, its diaphragm sinks.
But at night, when electricity is at its cheapest, that water is run through a chiller, and as it chills and re-enters the tank, the diaphragm rises. By morning, the diaphragm is at the top, and the water is ready to circulate through and cool the building."
Tension Tarps and Pond Liners
Inside Bruco, Monolithic Airforms also makes specialty tension tarps and pond liners, using polyester vinyl fabric.
Tension tarps are covers shaped to exactly fit an elaborate, very expensive machine or piece of equipment. Because the tarp conforms around angels, it provides maximum protection from the elements.
A tension tarp was recently purchased by the SOAR Project that is assembling a huge telescope atop a mountain in Chile. SOAR tented their construction site with the tarp. It protects the workers, their equipment and the fragile telescope parts from 50-mph winds.
Pond liners manufactured by Monolithic Airforms are most often used to prevent chemically treated water in recreational pools from disappearing into the ground. But such liners are also sometimes used to keep something dangerous – such as arsenic – from leaching out of the ground and into the water. In either case, the nonporous polyurethane used for these liners does the job.
Compost Covers
Inside Bruco, Monolithic designs and manufactures Odor Free Compost Covers (odorfreecompostcovers.com) to fit a client’s specific needs. The needs can range from those of an amateur gardner striving to be more green to a city administration solving waste management problems.
We make the covers of a high-grade, moisture-proof, specialty fabric that confines offensive odors but lets water vapor and normal air molecules to escape. Such a cover allows and promotes the biodegrading of organic matter into a usable recyclable soil aid in a very short time.
The Odor Free Compost Covers are being made for and exclusively sold by MOR, Inc. For more information, please contact John Bouey via email visit his website.
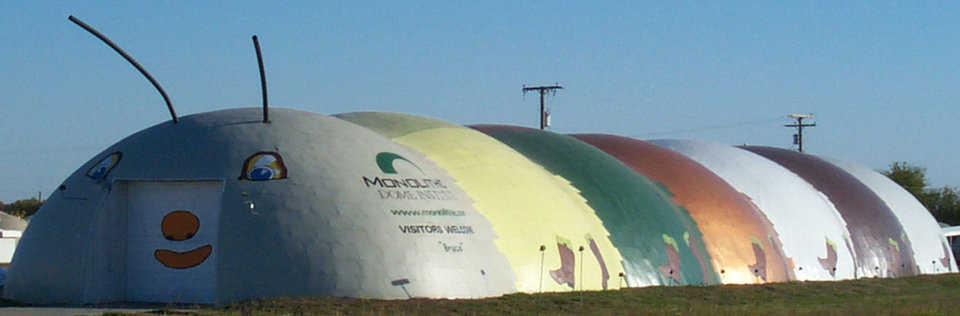
Makeover — In Summer 2001, Bruco got a makeover and now has a multi-colored coat to complement his flirty eyes, smiley mouth and glow-in-the-dark cowboy boots.
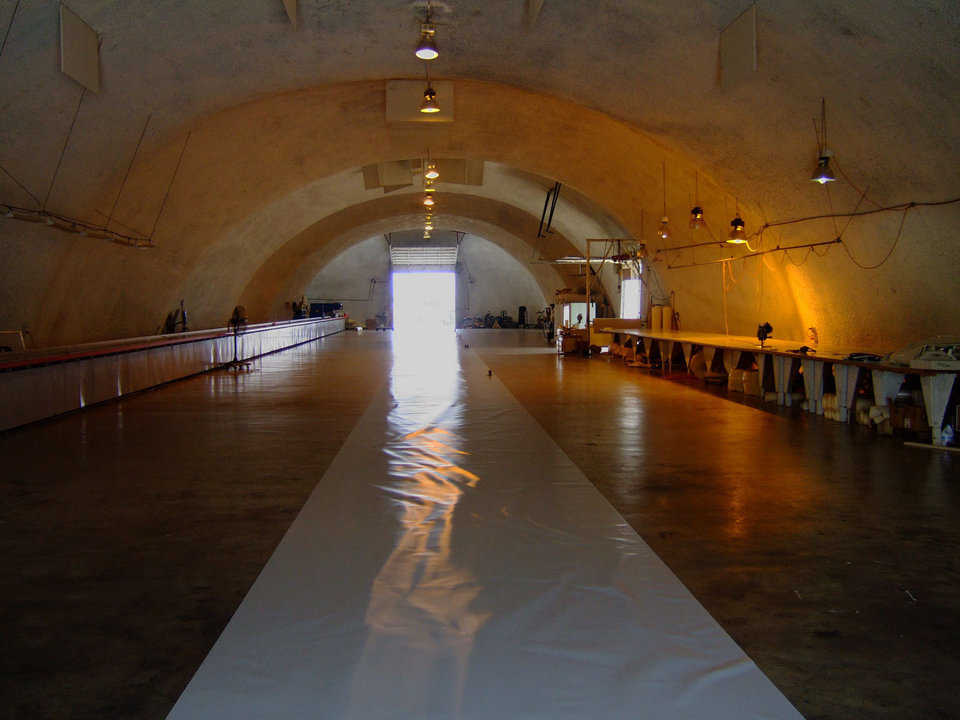
Inside Bruco — Bruco’s openness provides room for the manufacture and assembly of an Airform for a 200’ diameter Monolithic Dome, a 300’ diameter Crenosphere, or a grain tarp to cover a 2-acre grain pile.
A/C Unit — Everyone knows that in Texas you “Go big or go home!” Even the weather is extreme—we sometimes have as many as 50 days in a row that are one hundred degrees or hotter! Anybody that knows anything about air conditioning will tell you that a five-ton air conditioning unit cooling 14,000 square feet is ludicrous – any place but in a Monolithic Dome where this five-ton air conditioning unit has been cooling off the 14,000 square foot, “Bruco,” Airform manufacturing facility in the Texas heat for about 22 years.
T5 Lighting — T5 lighting provides Bruco’s 14,000 square feet with both efficient light, as you can see in this interior picture, and heat. Winters in Texas can be cold, but Bruco has no traditional heating system in place. In the winter, we leave the lights on at night and between the lights and the RF welders, the building stays warm. (Note: The fan shown in this photo is used to dissipate the odor caused by the man hand welding an Airform.)
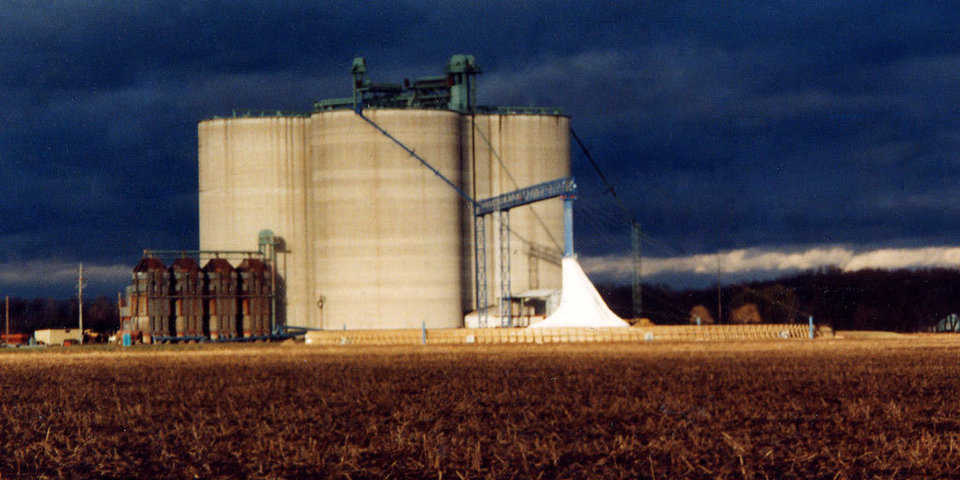
Grain Cover — It’s totally assembled and ready to start receiving grain. Center tower supports the grain conveyor that fills it. Grain drops through the center tower and under the cover.
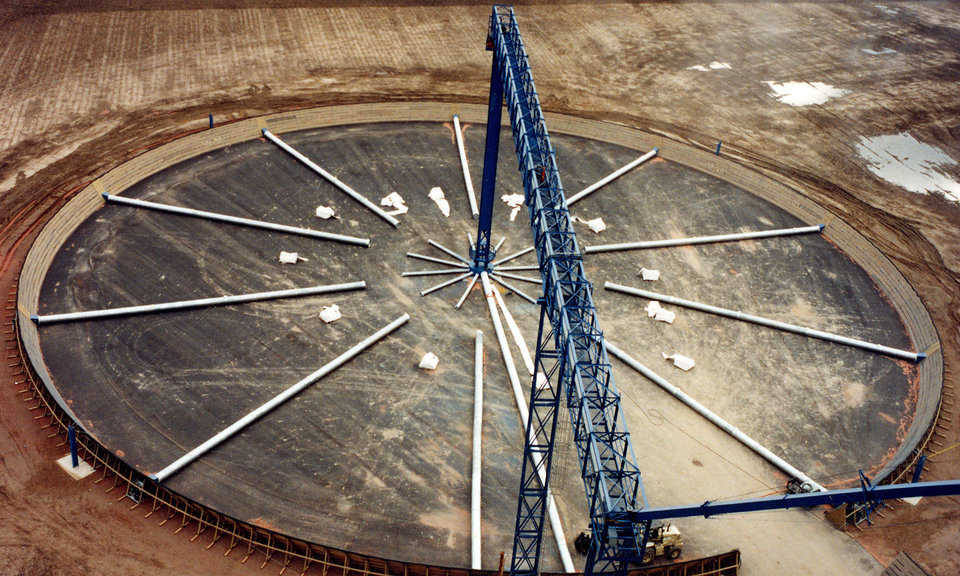
Covered outdoor grain piles — They are usually fenced around the perimeter, with aeration ducts laid in a spoked wheel pattern. Those ducts maintain an even temperature and help keep moisture down inside the grain pile. The grain cover sections, shown above, are ready to be rolled out and fastened together.
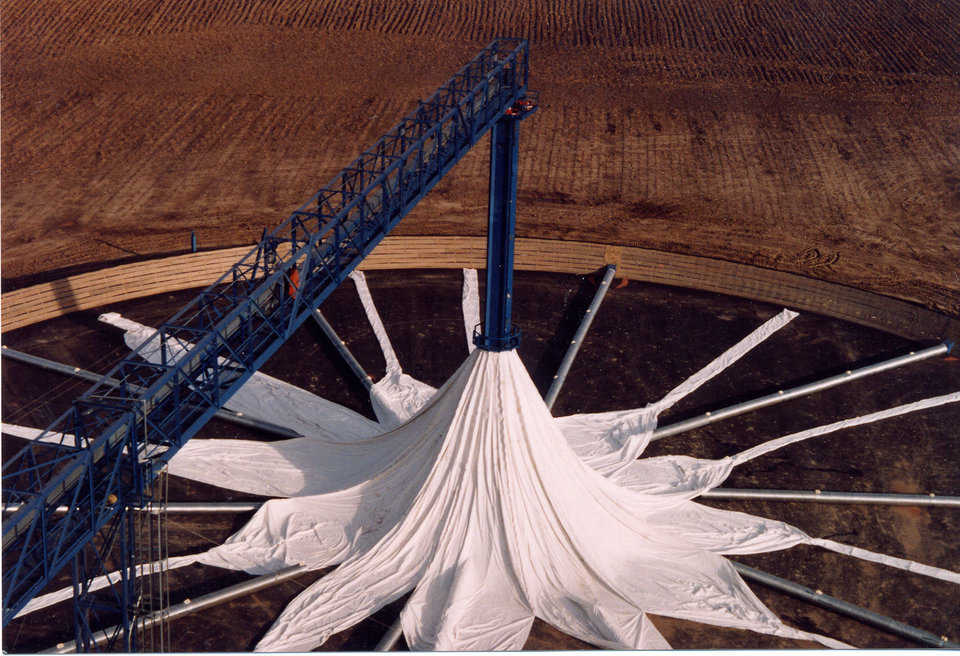
Partially assembled grain cover — Each of the gores (sections) is fastened to a lifting ring around the center tower. As the lifting ring rises, the gores attach to each other.
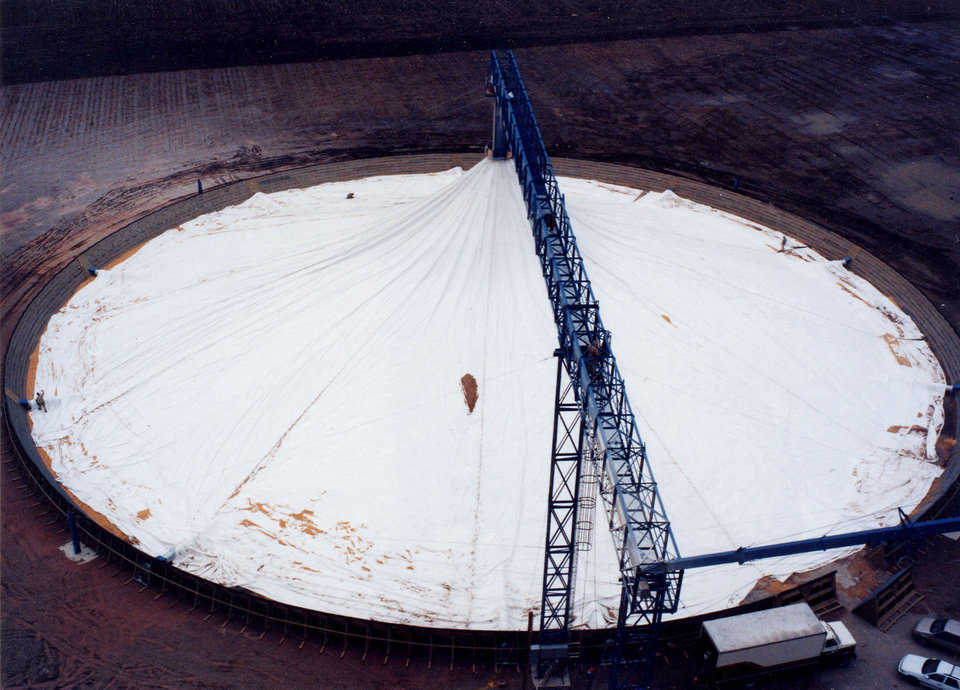
A completed grain pile — Grain is spread to the edges forming a weather tight storage.
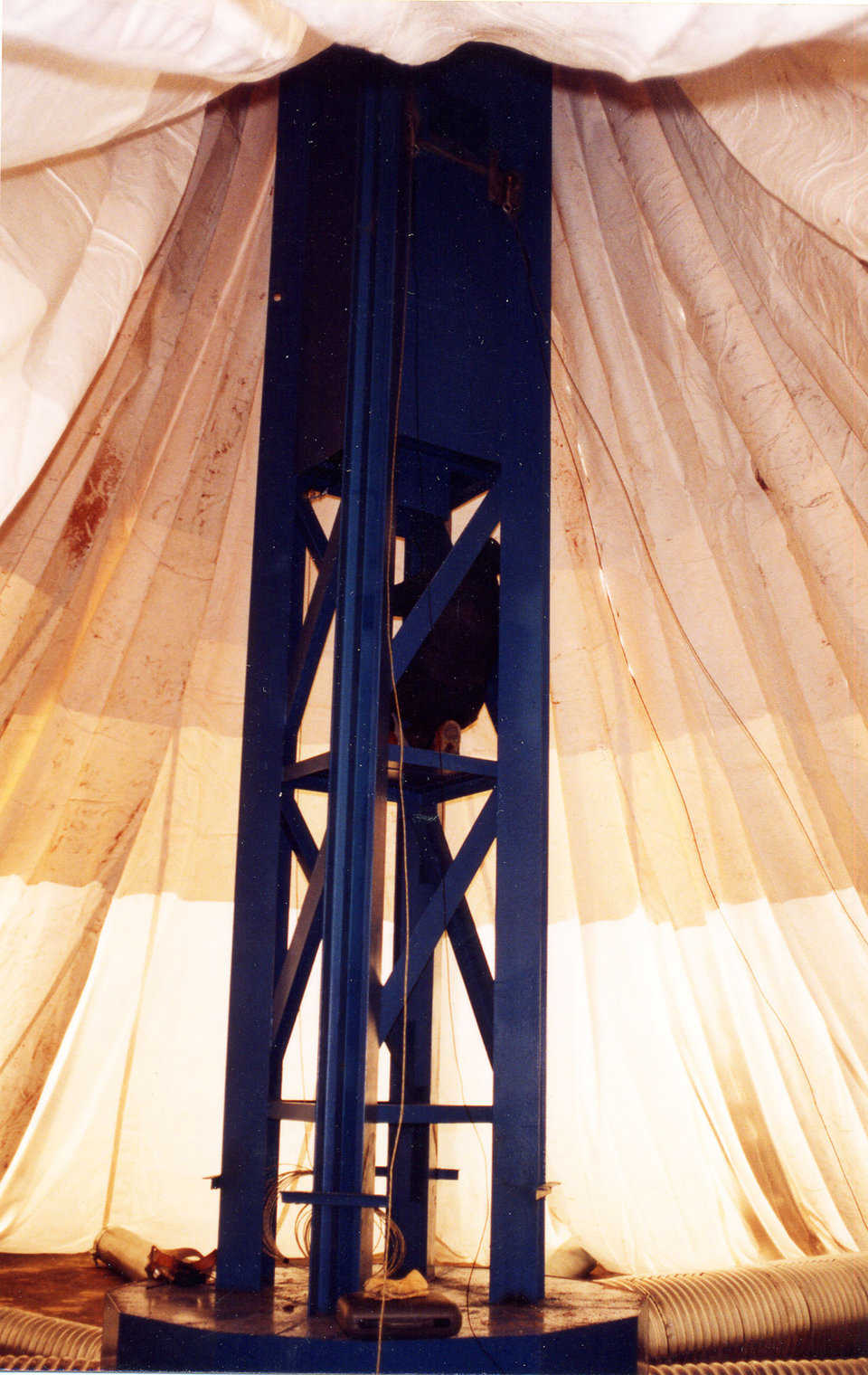
Center tower — It supports the grain conveyor that fills it. Grain drops through this tower and under the cover.
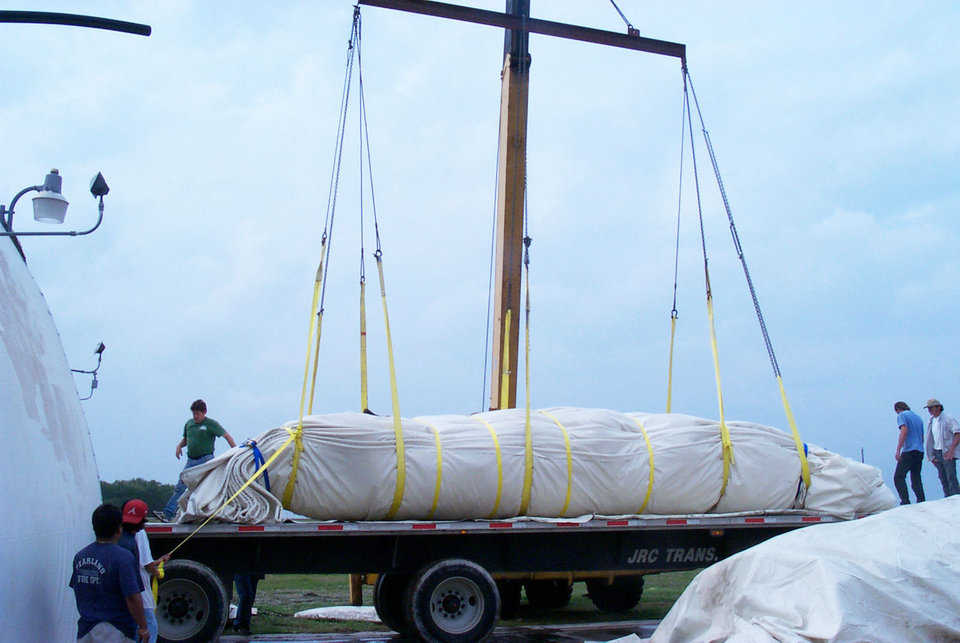
Loading a Monolithic Dome Airform — Don Garrison, Airform Division Manager, and workers use a crane to load the 265-foot half-sphere Airform created for Hovensa, a coke storage facility in St. Croix U.S. Virgin Islands.
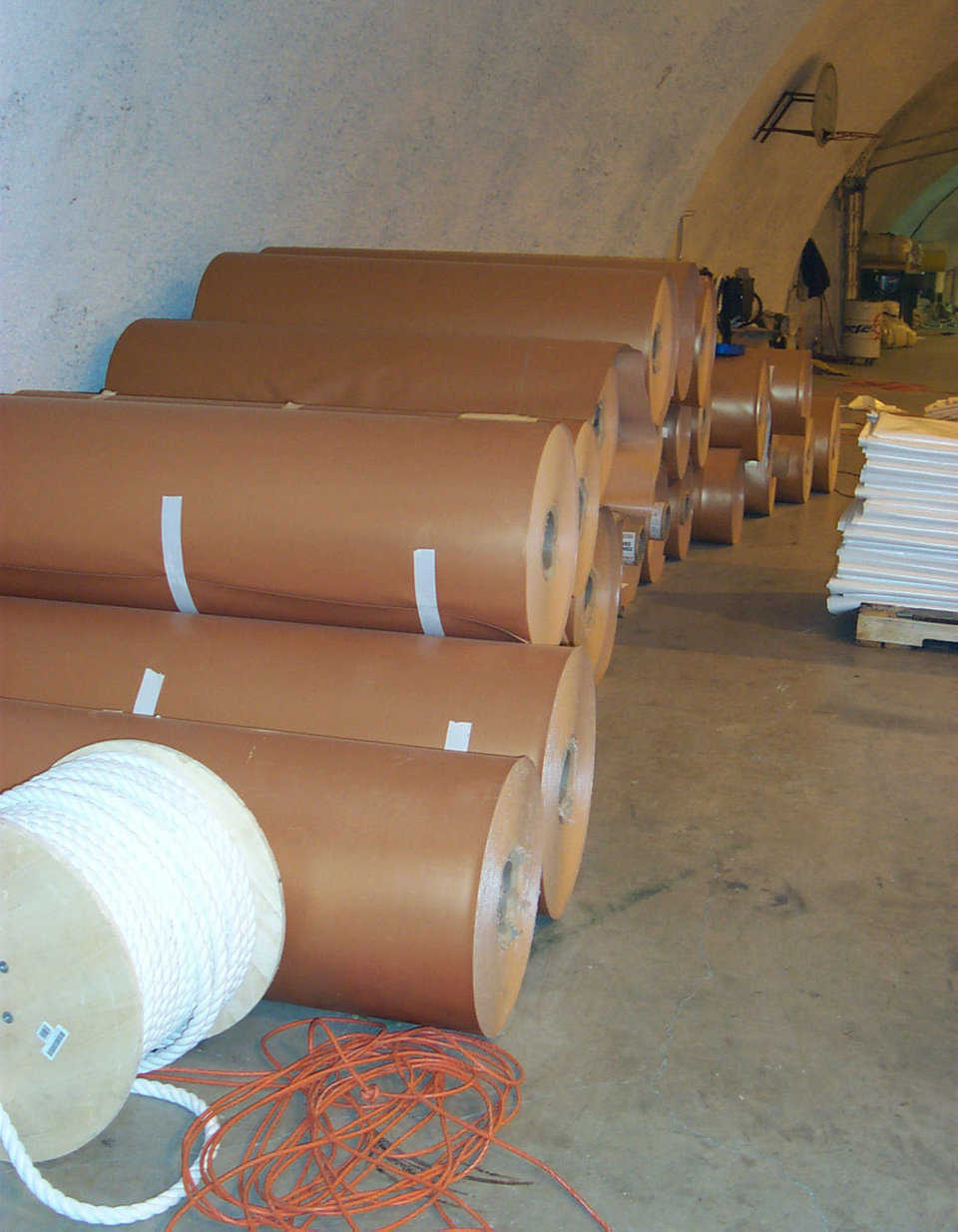
Airform fabrics — Monolithic has special fabrics shipped to Bruco from all over the world. Bruco safely stores massive rolls.
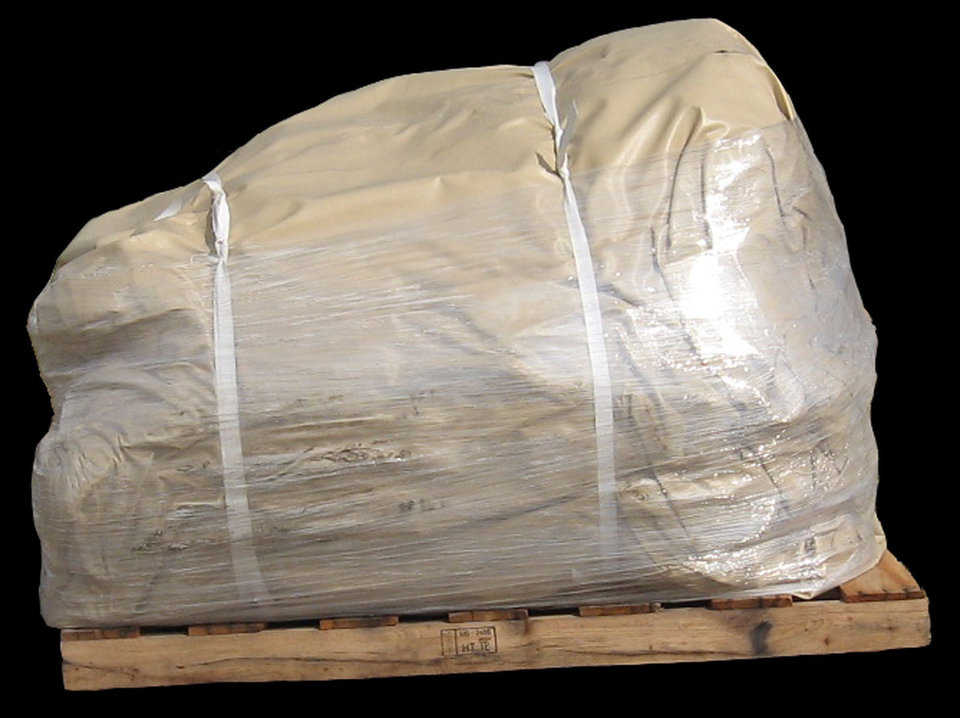
Going my way? — The shipment process includes properly folding an Airform and covering it with scrap fabric and shrink wrap.
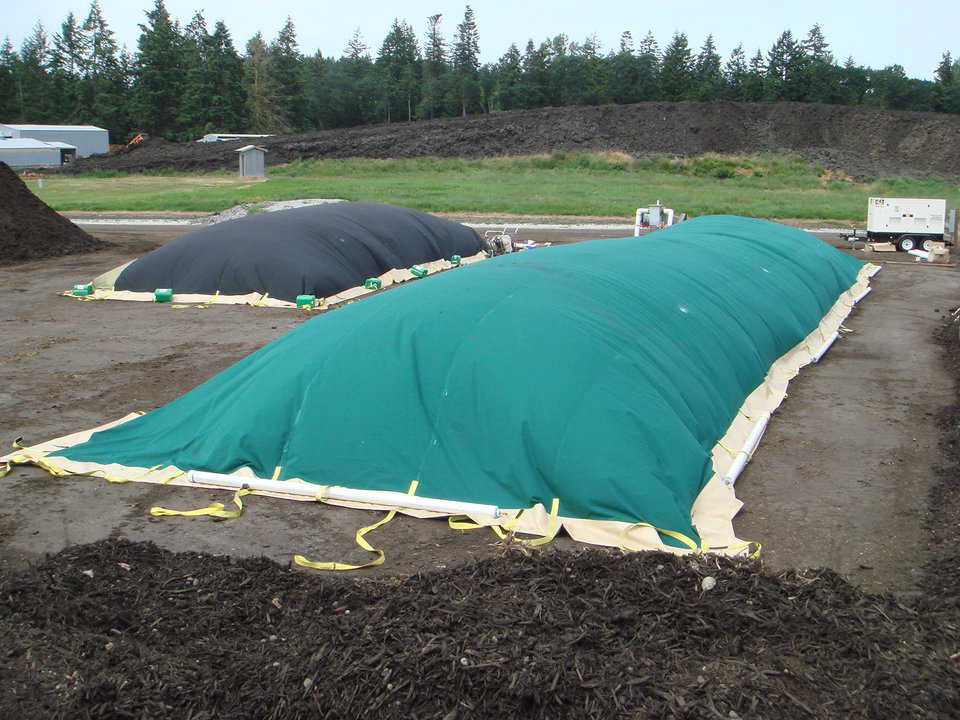
Compost Cover — Manufactured in Bruco, these compost covers create an odor free option for the composting industry and home composters alike. See www.odorfreecompost.com.